I've been reposting a series I wrote during my move from LA to Oklahoma on commercial aviation. I've previously discussed business models, airplanes, route networks and loyalty programs. But today, I'm going to be talking about safety.
I should start talking about safety by emphasizing that air travel is very safe. It’s about an order of magnitude safer per mile than a bus or a train, and two orders of magnitude safer than a car. There is literally no safer way to travel long distances, and a tremendous amount of work goes into that, because an airliner is massive and complex, and is constantly trying to break. This post should not change your opinion about flying, but if that’s something you’re really nervous about, you probably should stop reading now.
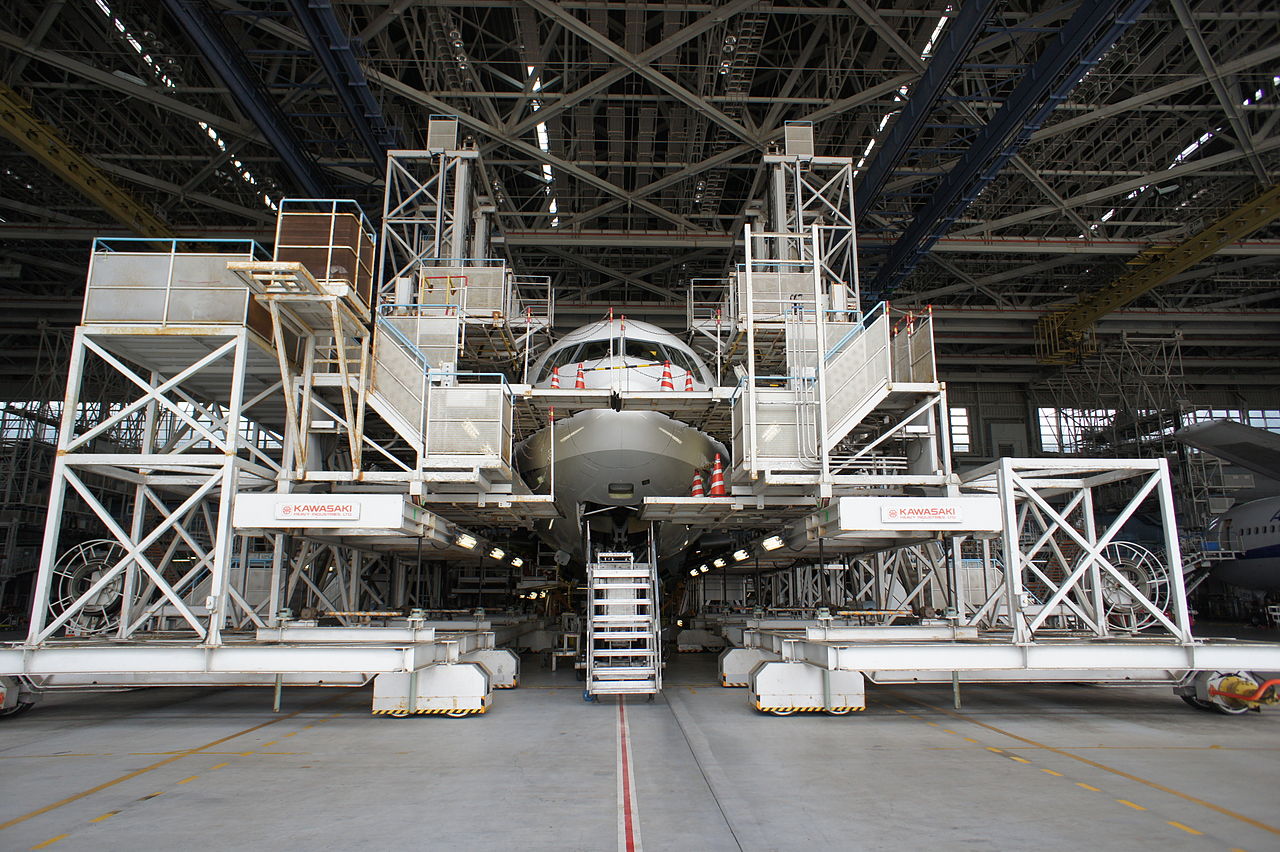
My previous job was as a small cog in the machine that sees potential safety problems before they get out of hand, and fixes them. I’ll outline the process I participated in, using a composite from various issues I worked:
Aluminum is a wonderful material. It’s light and strong. But it also cracks easily. So there are hundreds of required inspections done at various intervals on every airliner out there. One day, during one of these inspections, someone notices a crack in a fitting in the wing root. It’s rather large, so they call their engineering department, which looks at it, measures it, and checks the various manuals which tell them what they can fix on their own. (It’s said that an airliner is ready when the weight of the paperwork is about the same as the weight of the airplane, so there are a lot of those.) They decide they don’t have the authority to fix it, so they call the manufacturer. This is called an AOG (Aircraft on Ground), and it’s a big deal, because the airline isn’t making any money on the plane while it’s doing that, which tends to make them cranky. The manufacturer has a team of engineers who look it over and come up with a quick-and-dirty fix to get the plane back into the air. (In this case, quick-and-dirty means that they have to watch the area very carefully to catch any further cracking, but so long as nothing is found, it’s safe.) They then go to the next crisis, which is probably a truck running into a different airplane on the other side of the world.
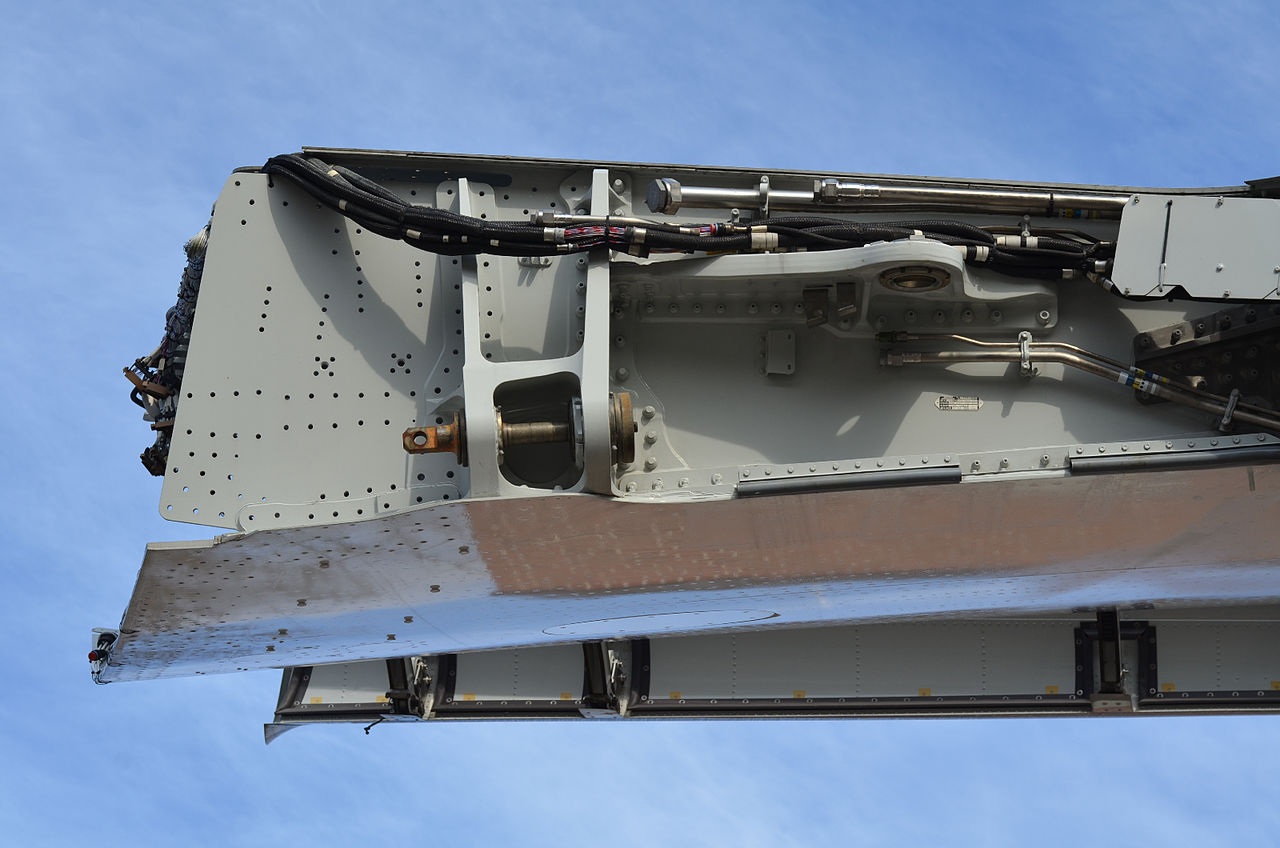
The reports from the wing root crack get turned over to another group, which analyzes them to see if there’s a systematic problem. Maybe the designers were a bit too aggressive when they did the fitting in question, and it needs to be replaced with a new design. So the design group is called on to figure out a better design. If the plane is still in production, the most important thing is to change the part being put on in the factory.
After that, a service bulletin is issued to change the aircraft that are already in the fleet. This is the legal vehicle for making a change to an existing airplane. There’s a tremendous amount of regulation around the configuration of airplanes, to make sure that nothing gets on that isn’t approved. I've heard that it's easier to put something into a person as a medical device than it is to put something onto an airliner. There’s a group of engineers who figure out how and when to make the change, and what other alternatives the airline might have, and then they hand it off to another person to write up (my old job). This is not as easy as it sounds. It’s a legal document, which means it has to be written very precisely to make sure that the airlines have to do what the manufacturer wants them to do, and it’s going to be going to airlines all over the world. Also, the FAA, who approves it, has very strict standards. And engineering is constantly refining their solution, often up to the last minute.
Eventually, the bulletin goes out. In this case, it mandates new inspections for cracking in the fitting, and if there is cracking, or if the airline wants to get out of the inspections, gives instructions for changing to the new fitting. A team goes out and makes sure that the replacement procedure actually works. (This is much more helpful than you’d think. Even the best drawings/computer models are sometimes inadequate, and when the plane in question is old and has a bunch of changes in the area, it’s impossible to know what the fleet looks like without going out and looking at it yourself.) If it doesn’t work, then a revision is issued. The FAA mandates that the bulletin be done, and the world’s other aviation authorities follow somehow. (I’m not actually sure how.)
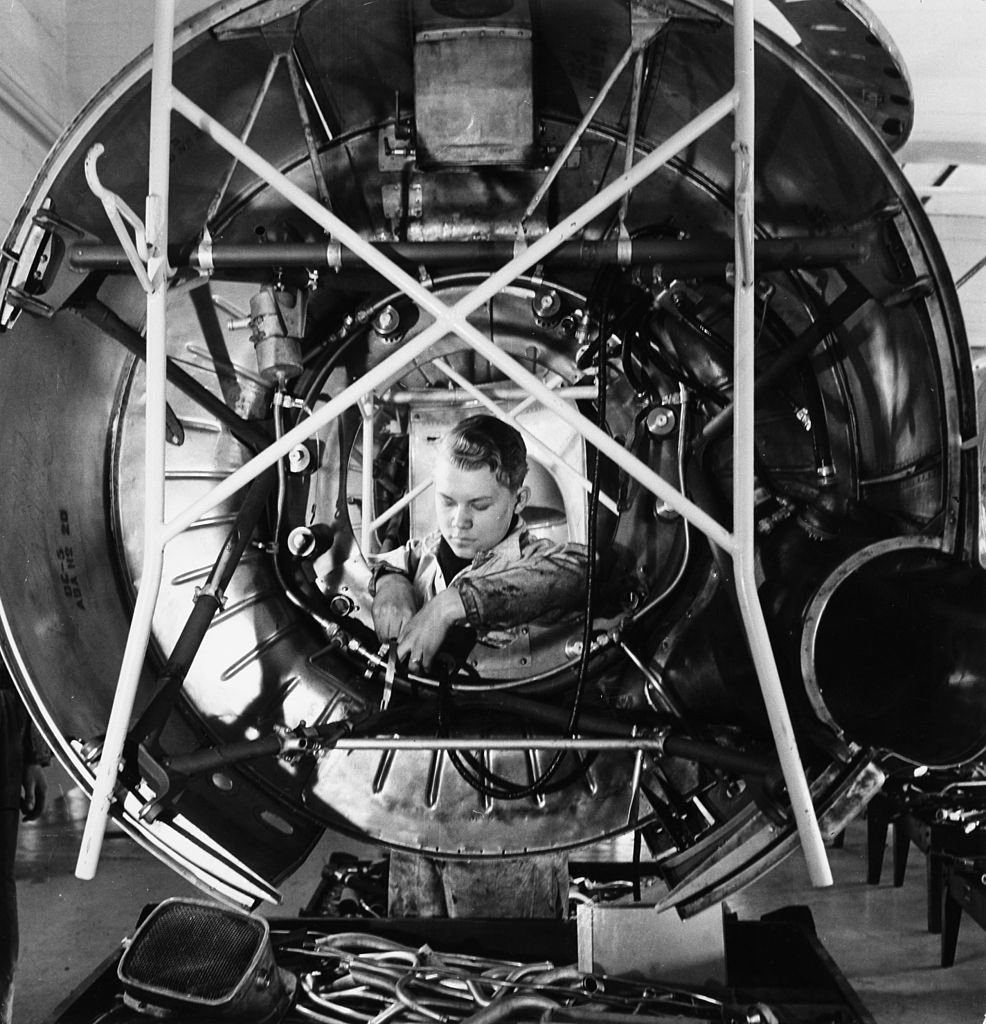
20 years later, the airplane is out of production. Someone is doing another routine inspection in the area, and discovers a crack in the wing skin. They call the manufacturer, and more analysis is done. This time, they discover that by stiffening the fitting to stop it from cracking, they moved the stress into the wing skin, which is now cracking. This is obviously very bad, and alarm bells begin going off. A high-priority project is put together to get the wing skin in that area inspected before there’s an actual failure. This could mean that an SB is out and mandated by the FAA in a matter of days (normal time from project start to mandate is ~2 years), but that’s pretty rare. Usually, the first pass goes out with instructions to contact the manufacturer if problems are found, while a second round is done to figure out a long-term solution that can be written up in a revision to the Service Bulletin. The airlines are interested, as they want a solution that is as cheap to implement as possible, preferably one covered by the manufacturer. (The warranty is long expired, but that doesn’t stop them from asking.) Eventually, the chosen solution involves disassembling part of the wing, removing a whole section of skin, and reinstalling a replacement. This is annoying, and leads to an early retirement of part of the fleet. This is seen as good news by some people at the manufacturer, as it’s fewer of the things they have to support.
This same process happens on every other part of the airplane. Every part of the next airliner you get on is rigorously certified, carefully inspected, and everything is documented to make sure that no problems are missed. Yes, occasionally an airline messes up and flies a plane that isn’t fully compliant. But this is ultimately a non-issue. Everything is chosen to be very conservative (the inspection standard is to give two good chances for crack detection between when the crack becomes detectable and when it gets critical), so the only damage is to the airline’s bottom line when the FAA notices. Airlines outside of the western world are not always so careful to comply with safety directions, although the major international airlines are pretty good.
Ultimately, air travel is the safest means of transportation yet invented, and a tremendous amount of work goes into keeping it that way. I've given a moderately detailed look at one specific type of issue, but there's an army laboring to make sure you get to the beach or that important meeting safely the next time you fly.
Comments
Nice description Bean.
It has almost become a cliche when we in the industry speak of the safety underpinning that goes into building, maintaining, and operating an airliner. Yet it is true, and the remarkable oversight that goes into the operation is deep and broad.
On the occasions that I chat with passangers about this, I tell them that the complexity of delaying or cancelling a flight (not to mention the grounding of a fleet like the 787 battery issue) can be staggering--almost too difficult to imagine and grasp in fact.
An aircraft that is taken out of rotation/service will require a replacement as a minimum or even an equipment sub. But if that call is made it means that it is done most often based on safety. As we know, we all want (particularly the airlines) for the pax/aircraft flow to run uninterrupted. It is when disruptions are made to that flow that problems arise. Lots of cool modeling done by researchers on how these complexities grow. I know the passangers are frustrated, but I still am in awe how quickly (usually within 24 hours) a place like O'Hare can regenerate itself after a disruption like a massive snow storm.
On the maintenance side, if an AD is fired out that requires immediate action with groundings and delayed flights the passangers are indeed discomfited jbutust like in a snowstorm, but it gets back to normal remarkably fast considering all thgat is being done behind the scenes to compky and repair.
I know the airlines get the reputation of wanting to get things done as inexpensively as possible, but they realize that trying to get by on the cheap too often is sailing awfully close to the wind. If they lose an aircraft and are found negligent/culpable then it could, conceivably, drive the company out of business. All stakeholders in the system work to avoid that and keep safety at the fore.
I would argue that the reliability, pretty decent schedule adherence (I know, not perfect), and safety make modern air travel a marvel of the modern world. It is simply economic infrastructure. Yes I wish it could be more pleasant with bigger seats, but it ain't too bad for what it does and that is move millions of people every 24 hours.
Hear, hear!
And for anyone who wants to start talking about the glory days before deregulation, remember that yes, the seat was bigger, but it cost twice as much.
Actually, you fly for the airlines, don't you? I'd be interested in a pilot's perspective on the industry, as that's not a side I've dealt with much.
I would be pleased to weigh in with a pilot's view. Let me know what aspect would be of interest and I will draw something up. `Lots of facets to an industry that, just domestically alone, moves the equivalent population of Philadelphia to Minneapolis every 24 hours--and that was at the year 2000 so I am sure that it has increased. Engineering, maintenance, actually operating the aircraft, flow controls for the ATC system, etc. It still amazes me how well it works.
That's up to you and whatever you want to talk about. If you want, I'd be happy to let you extend this series, which is currently going to end with Part 7. The remaining parts are a discussion of hubbing by my sister (who is very interested in airlines and airport management) and a look at the Asiana crash at SFO and Air France 447 by me.
Sounds good. If you don't mind dropping me an email I can foward an idea or two to to you.
Btw, I gave a presentation last year on AF 447 and you are welcome to the audio of this (did not have a visual recording) should you wish and if I can find it.
Bill Palmer's (A Delta check Captain) book on this is outstanding and discusses the specifics of the Airbus flight control "laws." My presentation was for a general audience however, and does not get into specific details about the reversions etc. that occurred.