The main tasks of the naval engineer once oil and turbines had been adopted were making the existing plants more powerful and more efficient. The most obvious way to resolve the mismatch between the desire of turbines to turn quickly and the desire of the screws to turn slowly was to use gears.1 The problem is that transmitting tens of thousands of horsepower through gears is not easy.
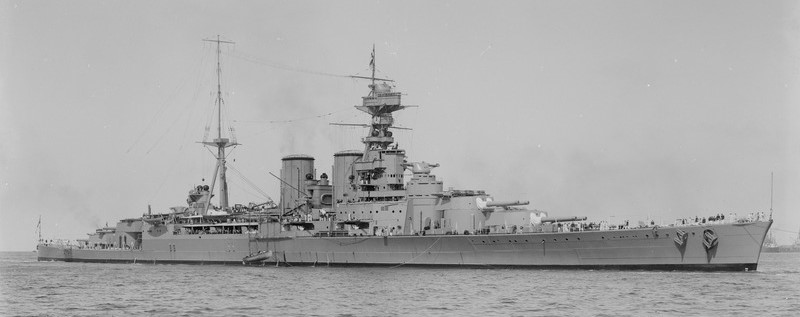
HMS Hood, the first battleship designed with geared turbines
The geared turbine first went to sea in large ships in 1916 with the three ships of the Courageous class, although they weren't technically battleships. This was necessary to allow them to make 32 kts, by far the fastest sort-of capital ships of the day. They also introduced new small-tube boilers, which were about 30% lighter for the power than the large-tube boilers in use previously. The first proper battleship followed a year later, when the USS North Dakota was refitted from direct-drive to geared turbines. But since there are very few details on that plant available,2 we'll look at the first battleship designed with a geared turbine plant, HMS Hood.3 She had separate high-pressure and low-pressure turbines on each shaft, along with astern blades in the low-pressure turbine casing. The outer shafts also had cruising turbines which could be clutched in at low speeds. At full power, the gearing reduced the 1500 rpm of the HP turbine and the 1100 rpm of the LP turbine down to 210 rpm at the shaft. Total designed power on each shaft was 36,000 hp, making Hood the most powerful ship afloat, although in practice turbines could be safely overloaded, and she made 32 kts using 151,600 shp on trials at a displacement of 42,200 tons. 24 small-tube Yarrow boilers produced steam at 235 psi, and 1,200 tons of oil could propel Hood 6,400 nm at 12 kts.
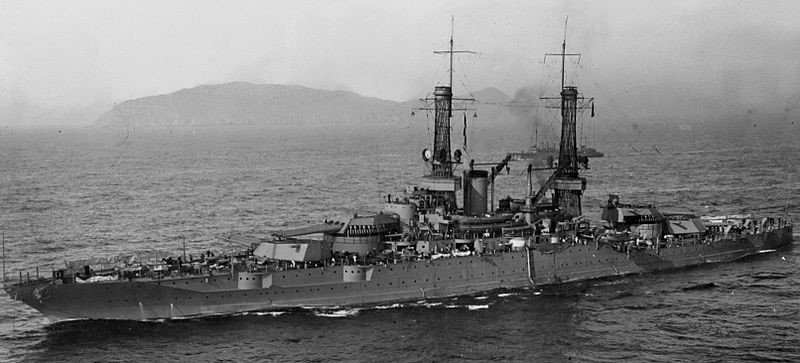
USS New Mexico, the first turboelectric battleship
The USN took a different approach to solving the efficiency problem, turboelectric propulsion. In this, the turbines turned electrical generators, and the shafts were turned by electric motors. This was first used on the battleship New Mexico,4 followed by the units of the Tennessee and Colorado classes. It was planned for the 1920s South Dakota class, and used on the Lexington class battlecruisers, two of which became the US Navy's first big aircraft carriers under the Washington Treaty. New Mexico consumed about 20% less oil at 17 kts than her direct-drive sisters, but the major advantage of turboelectric propulsion was that it allowed greatly improved internal subdivision, so the Tennessee and Colorado classes had some of the best underwater protective schemes of all time. It also meant that the motors could be near where the shafts entered the ship, reducing the chances of shaft damage causing flooding. A less obvious advantage is that turboelectric power allows the props to be reversed instantly by switching the power around, and for full power to be applied in reverse5 and sustained indefinitely.
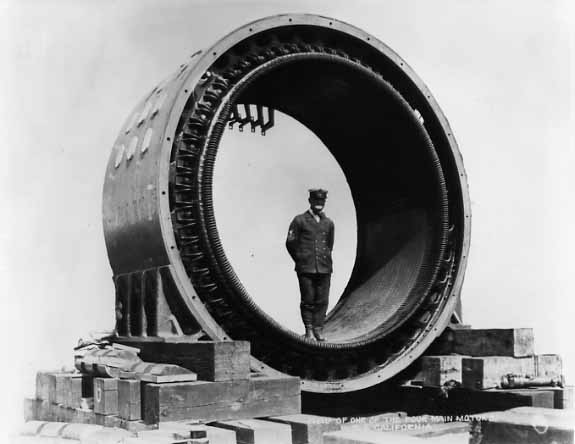
A motor winding from USS California
Turboelectric drive was not without its drawbacks. The most serious was that it was vulnerable to shock damage, which put several ships out of action during WWII, although power was usually restored fairly quickly.6 There were weight disadvantages, but they are often overstated: Lexington’s plant was of approximately the same size, weight and power as that of Hood, while West Virginia’s machinery was comparable to that of Royal Sovereign. However, turboelectric propulsion was not suitable for smaller ships,7 and the battleship holiday meant that development was focused on geared turbines. When new battleship designs were planned in the late 20s, turboelectric lost out on grounds of weight. It would have made the ship 20 ft longer and slightly wider, and cost a 21 kt design about 0.5" of deck armor. Later, during the studies leading to the North Carolina class, a turbo-electric plant was considered, but according to Dulin & Garzke, it was discarded as 180 tons heavier than the double-reduction geared plant ultimately chosen.8 The Germans, however, revived it with the intent of using it on the Bismarcks, although they switched to geared turbines before the ships were laid down.9
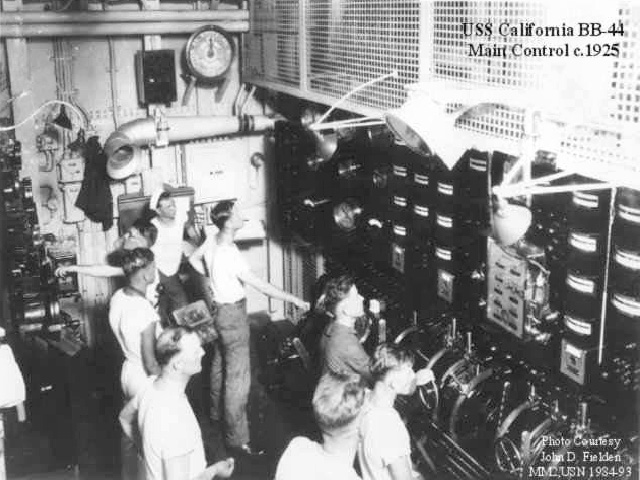
The control room aboard California
During the 30s, the temperatures and pressures used in power stations ashore climbed rapidly. In the US and Germany, naval turbines were built by the same firms that built them for use ashore, and steam plants gained rapidly in power and economy. The British bought their turbines from specialist naval engineering companies, and saw their traditional edge in that field reversed. The biggest innovation was the introduction of superheated steam. When water is first boiled, it is known as saturated or wet steam, because it remains at the same temperature as the water and retains some moisture. When steam is heated above the boiling point10 it is known as superheated or dry steam. Superheated steam carries more heat per unit mass, which in turn can be extracted by the turbines.
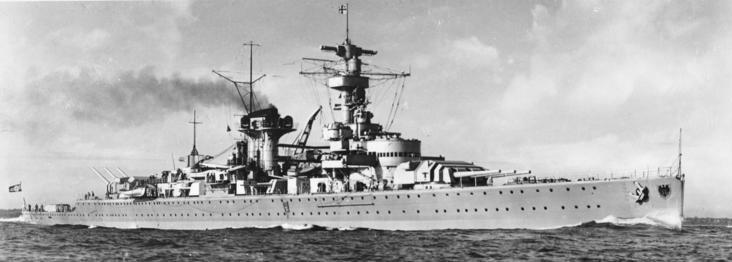
Panzerschiffe Deutschland
In the 30s, competition to the steam turbine began to emerge in the form of the diesel engine, although ultimately no battleships were built with them.11 Diesels offered improved fuel efficiency, particularly at low speeds, but they were too heavy and bulky to compete with steam plants in battleships. The Germans did use them in their Panzerschiffe of the Deutschland class, but these were essentially cruisers fitted for long-range raiding. The Japanese originally planned to use diesels on the Yamato class, but the test installation proved so unreliable that they abandoned them and switched to steam. The Germans actually developed diesels for their planned H-class, which would have had four engines on each of their three shafts. Each diesel would have produced 13,750 hp from 9 cylinders, a 65 cm bore and a 95 cm stroke.
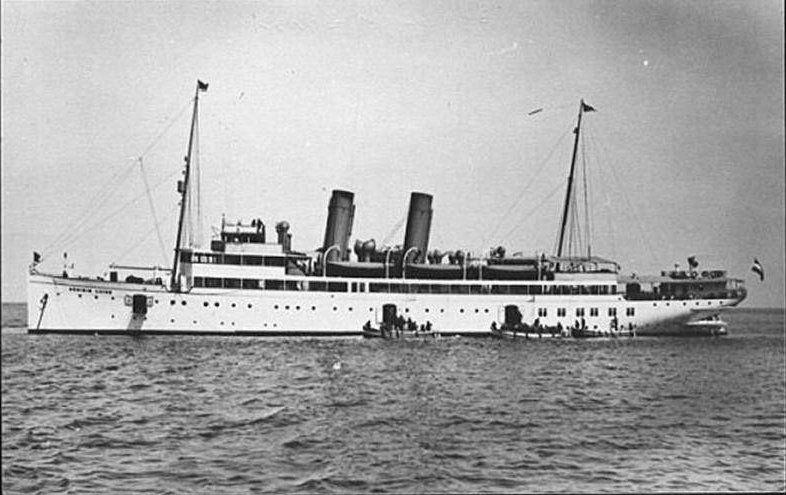
SS Königin Luise, fitted with hydraulic transmission
One minor note of some interest is the hydraulic transmission that was planned for the German battlecruiser Fürst Bismarck, although work on her never progressed very far. I have no details on this system, but it deserves a mention.
Next time, I'll examine Iowa's plant in detail, revealing the operating details of probably the pinnacle of battleship engineering. They'd come a long way from the days of trunk engines on the Warrior.
1 Interestingly, gearing was also used on the very first screw steamships because the engines in question turned too slowly, and had to be geared up. This went away fairly quickly as steam engines got faster. ⇑
2 I've looked pretty hard, but details are incredibly scarce. I believe this plant wasn't particularly successful. ⇑
3 Hood was essentially a fast battleship, despite the British classifying her as a battlecruiser. ⇑
4 The prototype was the collier Jupiter, which later became the USN's first aircraft carrier, Langley. ⇑
5 Normally, ships were limited in reverse power by the size of the reversing turbine, which was much smaller than the ahead turbine. ⇑
7 There were serious economies of scale in the equipment, so it was about equal for battlecruisers, slightly worse for battleships, and much worse for cruisers and smaller vessels. ⇑
8 Something smells off about this number. 180 tons is not a huge number when compared against the 2,580 tons of propulsion plant in the final ship. Unfortunately, Friedman doesn't give numbers on this. ⇑
9 Interestingly, electric propulsion has made a comeback in recent years thanks to improvements in power electronics. The USN was a century ahead of its time! ⇑
10 Remember that boiling point rises with pressure. ⇑
11 Diesels had been planned for the center shaft of the German Prinzregent Luitpold of WWI, but they were never installed. ⇑
Comments
We discussed this somewhat abortively on SSC, but: suppose we were making a large surface combatant today and gas turbines weren't an option. We'd definitely go electric (possibly diesel, possibly steam turbine driven) right? Given modern expertise and efficiency of electric drivetrains?
(If gas turbines were an option, I think you also said that given the time to work out the details you'd prefer LM-2500s driving turboelectric to what we have now...)
Modern (post-battleship) naval engineering is a scheduled topic, but probably not for a couple of months. (I want to get more of the battleship technical stuff done first.)
That said, there have been large improvements relatively recently (last ~30 years) in high-power electric propulsion, which means it's what I'd select for future large-ship propulsion. Warship capability is defined more and more by available electricity, and it makes it a lot easier to lay out the ship. Put some turbines in the superstructure, away from underwater damage, and other safely buried. Motors are hardened and relatively small.
What about diesel electric? This is a proven concept for the railroad industry, has anyone tried scaling this up for propulsion of a ship?
Also fix this sentence: During the 30s, the temperatures and pressures used in power stations ashore climbed rapidly during the 30s.
It was used on US submarines before and during WWII (IIRC, pretty much everybody else ran theirs with separate generators and drive engines until after the war, when it became ubiquitous) and on some other ships. The Cannon class DEs are the most prominent surface ships, although I believe there were others. AFAIK it was never considered for battleships.
Do you have any recommendations for books on naval engineering, as background? I'm not really looking for a textbook, but I guess I'd be open to that too.
Re electric allowing full reversing power versus the turbines: what is the practical importance of this? I can see it being useful for possibly preventing collisions like the Yorktown or some of the confrontations the Navy has had in the South China Sea, but otherwise I don't really see the practical value. Maybe full effort stops to try to evade a dumb torpedo?
Docking is obviously done very gently, and I imagine usually with lots of tugs, and the hull shape seems like it would dictate against prolonged reversed operation.
Anyways, I was wondering if this is a large tactical advantage, or more theoretical.
Addenda to the above: in modern commercial aircraft, and I think in air combat operations, changes in altitude are primarily used for generating separation in cases of possible converging paths. Thus TCAS generates altitude change orders, and most traditional fighter ops trade speed for altitude to maintain energy over the opponent. Because of this, speed changes are rarely used.
Naval warfare, especially traditional line of battle, cross the T type things, obviously has a different set of tradeoffs, both for gaining tactical advantage over the enemy and to avoid torpedos. However, it still seems like there would be a dominant strategy? Did they mostly use heading changes or thrust changes for this sort of thing? Did WWI/II subs make use of different depths for tactical purposes?
You've identified pretty much all of it, actually. It's great in theory, and it did come in handy when you needed to stop suddenly for one reason or another (avoiding collision or dodging torpedoes), but I'd personally classify it more as a nice side-effect than as necessary, and definitely not a huge tactical advantage. Do note, though, that the USN came very close to using turboelectric on the Yorktown-class carriers because they wanted them to be able to back at high speeds so they could land aircraft over the bow in case of damage.
AIUI, it was more heading changes. Ships are rather slow to respond to throttle (and I'm not really sure how TE did there relative to more conventional propulsion) and slowing down is also usually a good way to get hit.
They did, although (and I'm not an expert in this), they usually alternated between the surface, periscope depth (exactly what it sounds like) and pretty deep when they were trying to hide/evade.
@tonyc
Introduction to Naval Engineering is one of the very best books I’ve read in terms of coverage on any subject. Excellent detail on late steam plants (it’s written about 60s-era 1200 psi steam plants, but Iowa’s are very similar) and it helped a lot when I took thermo, too.
Unfortunately, it’s not particularly strong on history, and what I know of the later parts of the steam has been pieced together. There’s a decent book up through the early 30s called A Short History of Naval and Marine Engineering although it’s stronger in the early years.
@bean
That's awesome, thanks for the answers. What's the fully developed yaw rate for a battleship?
Also, your first link to "Intro to Naval Engineering" didn't parse correctly for me. Maybe it's a misformed link? I did extract the Amazon item number manually though, and it's on my wish list.
@RedRover
I’ve fixed the link. Not sure what went wrong there.
Iowa had a tactical diameter of 814 yds at 30 kts, which comes out to 2.38 deg/sec. The Iowas were considered pretty maneuverable for ships of their size, and that’s without using differential throttle to tighten the turn. On the other hand, maneuvering of any kind scrubs speed, and putting half the engines into reverse scrubs it really fast.
I can second the recommendation of Intro to Naval Engineering, a truly fascinating book.
Bean: is there anything particularly interesting to be said about the difficulty of gearing/gear manufacturing (I wasn't aware gear-cutting equipment could be in short supply?) To a non MechE, it seems like two large gears in some fixed ratio is a fairly simple construction project.
To be honest, gear-cutting isn't something I know very much about. It was definitely difficult, but I can't describe exactly why. I will look into that more and get back to you. Maybe as a column, because gearing production had a huge impact on things like the WWII escort programs.
I've looked around a bit more, and come up with at least a partial answer. The basic problem is that cutting naval reduction gears takes some large, expensive, and specialized equipment. Early gears at least were cut by hobbing, and a hob big enough to cut large gears (Hood's main gear wheel was 12' across) is not something you buy off the shelf. Building one is going to be expensive and time-consuming. The USN presumably didn't have the capability available in the 1910s, and the US was always pretty paranoid about importing that kind of stuff.
A couple things to note:
The problem was usually cutting gears of a certain size. For instance, the USN, when trying to build an escort for mass production during the Cold War, set a maximum gear diameter, which could be produced quickly in an emergency. (Of course, they blew right through the cap....)
Buying more big gear-cutting machines in wartime is going to take capability from the specialist heavy machine tool builders. Their output is critical to lots of industrial expansion, and the skills involved are not easy to duplicate.