One of the less obvious problems of operating a warship (or any sort of ship, really) is fouling. The marine environment is an excellent one for all sorts of organisms to grow, and many of them find the outer hull of a ship a very congenial environment indeed. This is tremendously annoying to the operators of said ships, who would rather not haul around tens or hundreds of tons of barnacles, mussels, worms, plants, algae and various other organisms. They increase fuel consumption, reduce top speed, aid corrosion, and generally make a nuisance of themselves.
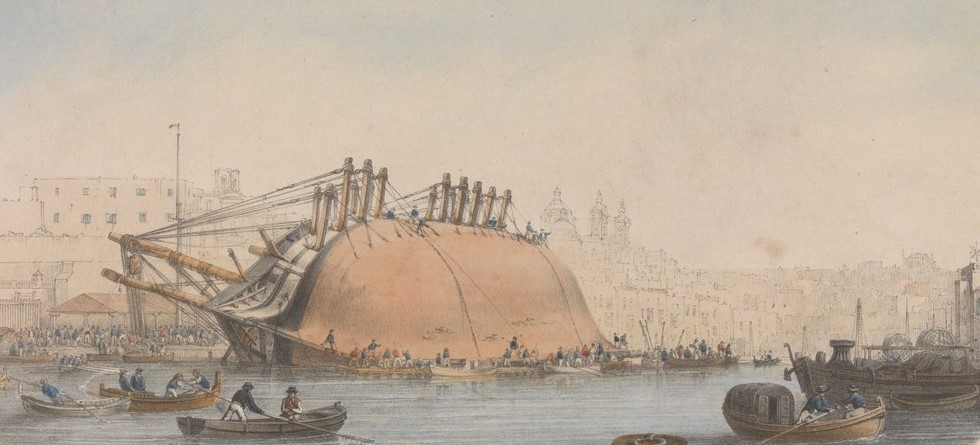
HMS Formidable is careened
Because fouling has been a problem for as long as men have sailed the seas, it's not surprising that attempts to control it also date back thousands of years. So far as we can tell, none of these methods were particularly effective against fouling per se, although many of them, like fitting the ship with lead sheeting, were probably intended to control shipworms instead, and worked reasonably well for that purpose. After all, fouling merely slows you down, while shipworms actually destroy the wood of the hull. Fouling was dealt with by somehow gaining access to the ship's hull and simply scraping it off. Today, drydocks are used for this work, but in the past, ships were often careened, beached at high tide and then tilted over to give access to the lower hull.
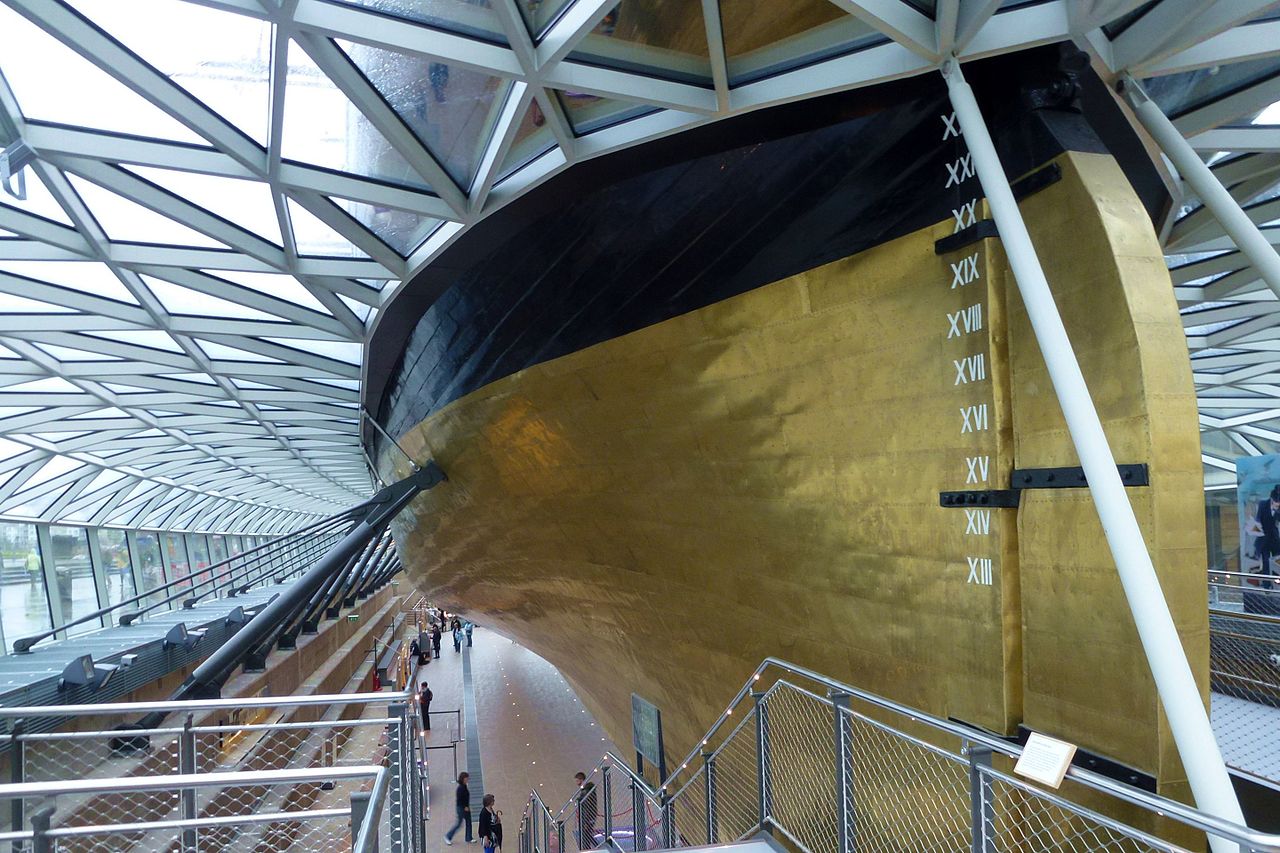
Copper sheathing on the clipper Cutty Sark
But shipworms remained a problem and grounding your own ship to scrape off fouling was annoying, so inventive minds continued to look for solutions. Lead sheeting had always been good at stopping worms, but it caused serious galvanic corrosion in nearby iron fittings, so in the mid-1700s, someone suggested trying copper, instead. A frigate, HMS Alarm, was fitted with copper sheathing in 1761, and sent on a cruise to the West Indies. When she returned, her hull was inspected, and the results were astonishing. Not only was her hull protected from shipworms, but she had also suffered almost no fouling. There were two main problems. First, the copper slowly dissolved and had to be replaced at intervals, a significant expense. Second, copper still caused galvanic corrosion of iron fittings, and some ships, including Alarm herself, suffered serious damage from this. Copper fittings could solve this problem, but they were expensive and it took until 1783 for the technology to be worked out, mostly by cold-working the bolts to improve their strength. This removed the last hurdle to large-scale coppering by the British, and after 1786, all RN ships were fully coppered. Other navies adopted this technology, though not so extensively. This ultimately gave the British a major advantage in the Napoleonic Wars, as their ships could remain at sea longer before their performance was sapped by marine growths.
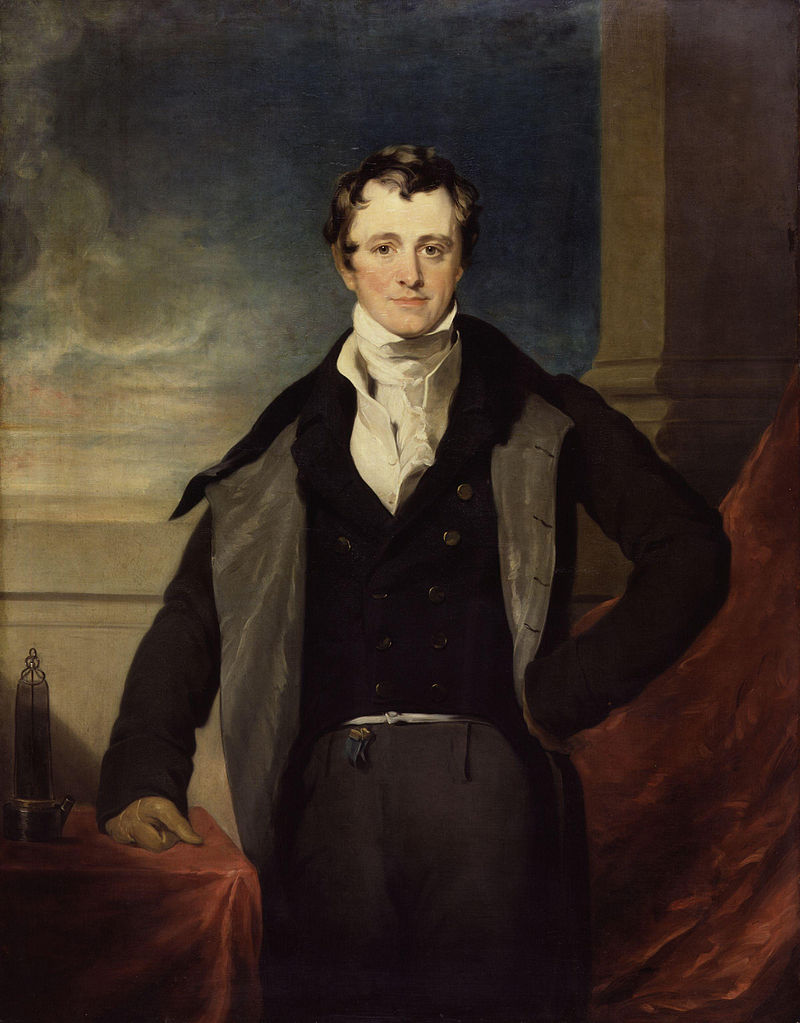
Humphry Davy
But this still left the problem of the dissolving copper. In 1824, the eminent chemist Humphry Davy announced that he'd found a solution. The copper dissolved by reacting with the seawater, and by attaching pieces of zinc, he could stop this dissolution and make the zinc dissolve instead. Unfortunately, when this was tried on actual ships, it turned out that while the copper didn't dissolve, it also didn't stop fouling. When copper dissolves in seawater, it produces copper oxychloride, which is toxic to most marine life. Davy's zinc stopped this process, as the zinc dissolved instead. Ultimately the RN decided that the expense of replacing the copper was worth it when the benefits of clean bottoms were taken into account. That isn't to say the field of anti-fouling was entirely static. In 1832, a new alloy know as Muntz metal was introduced. It was a copper-zinc (brass) alloy that was stronger and cheaper than pure copper, and corroded more slowly while still retaining copper's anti-fouling properties. Muntz metal and later alloys were also less susceptible to erosion from water and debris flowing past, an important factor as ship speeds rose.
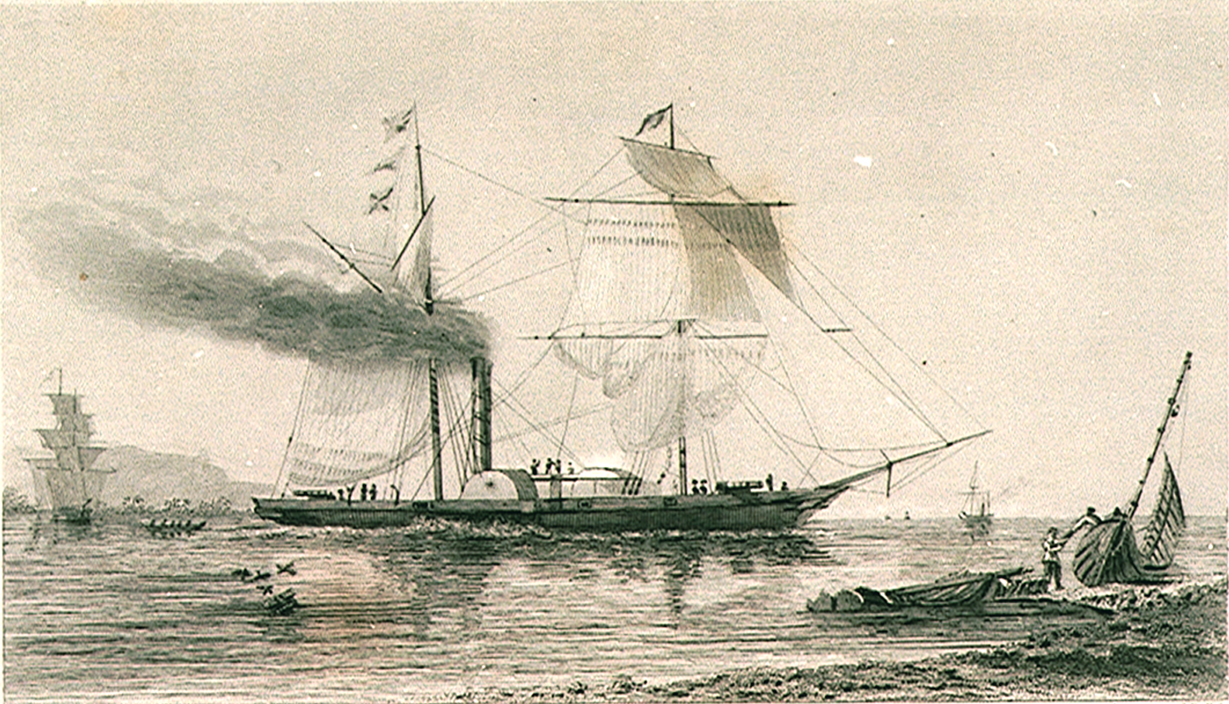
Nemesis, the first iron warship
And there matters rested until shortages of shipbuilding timber and the falling price of iron pushed people into building ships out of that metal instead of wood. It worked pretty well, except for two major problems. First, the iron hull obviously interfered with the operation of magnetic compasses, which were the basis of navigation at the time. This problem was eventually solved by the Astronomer Royal, George Biddell Airy, who used precise magnets to compensate for the ship's own hull. Second, an iron hull obviously couldn't be coppered without dissolving thanks to galvanic corrosion. To make this worse, iron turned out to be an even better place for various critters to grow than wood was. One early iron ship grew 9" of barnacles between docking in the UK in February 1847 and docking in Bombay that October. RN policy became to drydock iron ships in home waters every 12 months, while those in the Mediterranean had to be docked every 6. Fouling is more rapid in the tropics, and ships in the Indian Ocean had to be scraped clean every 4 months.
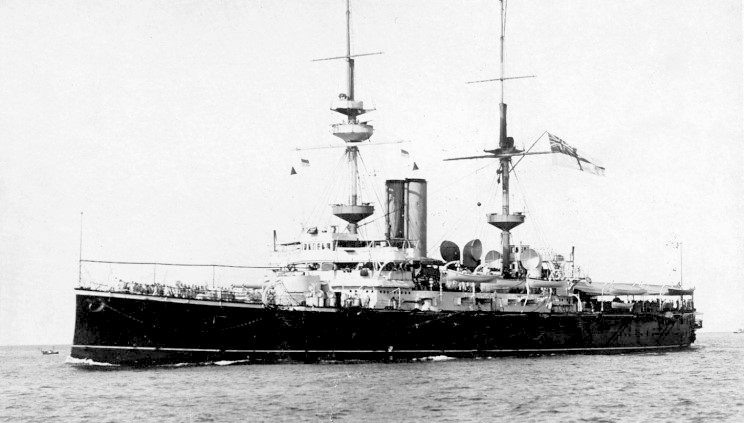
HMS Renown, one of the last sheathed British battleships
One possible way to solve this problem was to sheathe the lower hull in wood, and then very carefully attach copper to the wood, making sure that the nails holding it in place didn't contact any of the iron. This was expensive and heavy, and primarily reserved for ships that were to be deployed on foreign stations where drydocking was difficult. Another was to find some sort of paint that could keep the fouling off, which chemists began to deliver around 1860. These paints consisted of some toxin, usually based on copper, mercury, or arsenic salts, suspended in the paint, which would slowly leach out and kill any organisms attached to the hull. These worked reasonably well, although they were pretty effective at killing painters too, and by 1880, they had largely replaced sheathing.
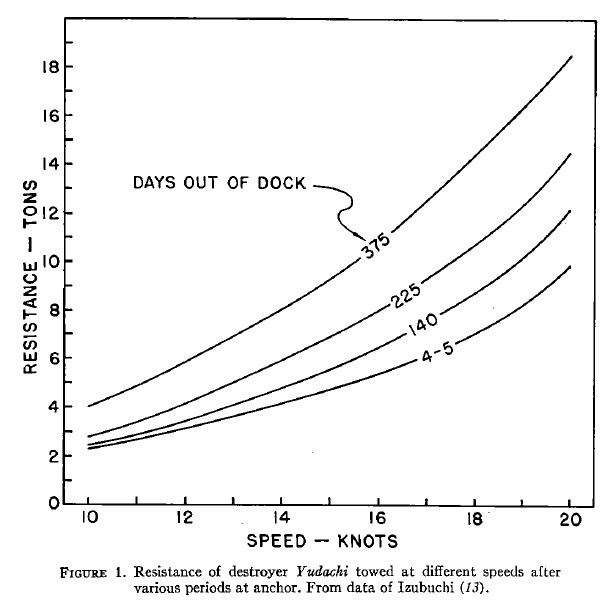
Data from fouling trials of the Japanese destroyer Yudachi
Early paints lasted about a year, and in northern Europe, a ship going in for scraping and repainting would usually need about 50% more power for a given speed than she would fresh out of dock. Fouling in tropical waters would double the power increase. The existence of useful antifouling paints spurred more research into the field. Initially, most of this work was done by private individuals hoping to supply both military and commercial customers, but the major navies set up their own laboratories to investigate the problem, and they soon overtook the commercial suppliers. By WWII, the USN was confident in going 18 months between drydockings, with minimal loss of speed or gain in resistance.
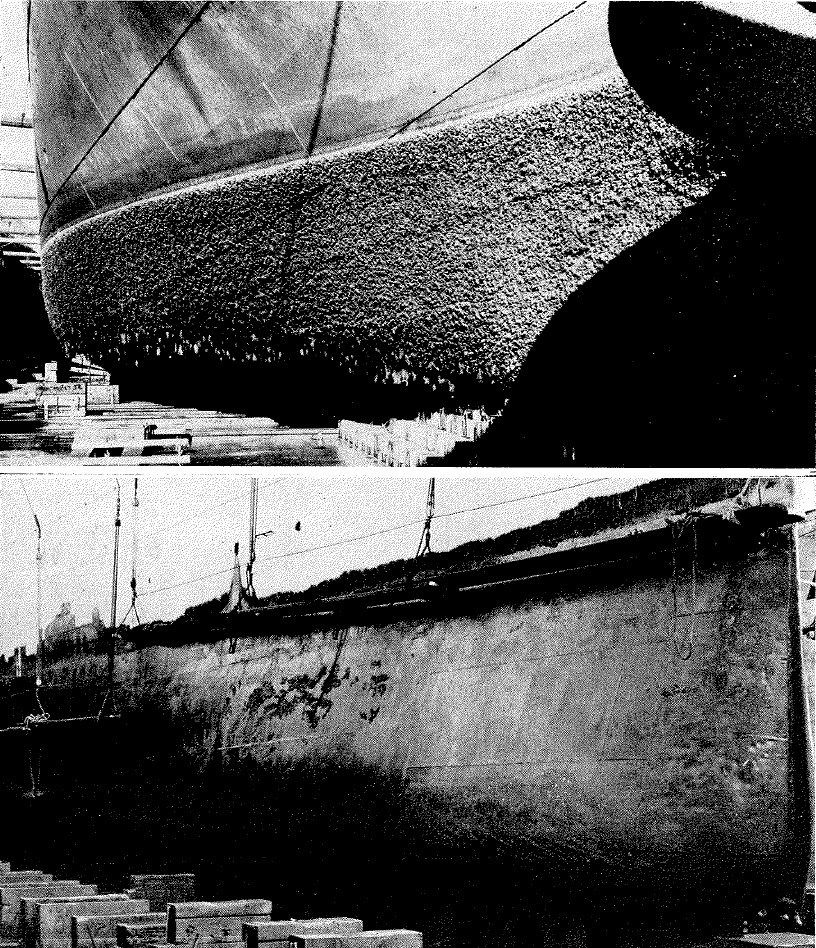
Improvements in antifouling paint during the WWII era. The top ship was afloat for 12 months, the bottom for 28 months with an improved paint.
Even after the war, development work continued, and in the 50s, a compound known as tributyltin (TBT) was developed. It was both effective and cheap, and by the 60s, it was the most common active ingredient in antifouling paints worldwide. However, scientists soon noticed that it had all sorts of other effects on the marine environment, including changing the sex of whelks. In 2001, a treaty was signed banning it, and scientists had to go back to the drawing board to find a paint that would protect both the hull and the environment. Today, most rely on copper-based biocides, although even these are coming under environmental scrutiny. A number of alternatives are being investigated, most of which emphasize using specialized surface coatings to stop organisms from attaching in the first place.1
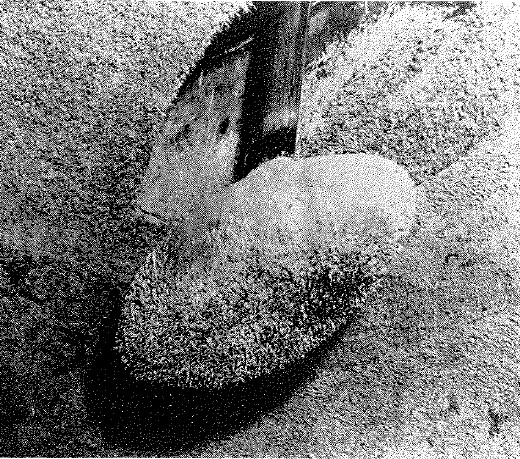
Fouling on a ship's sonar dome
The problems of fouling aren't restricted to the outside of a ship's hull, either. Sonar domes are particularly vulnerable to fouling, which can greatly decrease sound transmission and even create false contacts. To make matters worse, antifouling paints for sonar equipment can also interfere with the performance of the gear, although careful design can mitigate this. Another area of vulnerability is salt-water piping, which usually draws directly from the ocean. Fire mains are particularly susceptible to fouling, as the water is stationary in the pipes. Shipboard nozzles incorporate strainers to catch pieces of fouling that may be knocked loose, but they are of no help if the firemain is completely blocked by tube worms. Coatings are used to mitigate this problem, but regular inspections are still necessary. This is also a problem for industrial users of seawater, like power stations, who often solve it by keeping the water they use above 150°F, which kills off marine growth. Another problem that fouling poses is corrosion. While some fouling organisms do provide protection to the surface under them, barnacle shells usually cut into the paint covering the hull, exposing the steel to the seawater and causing massive corrosion.
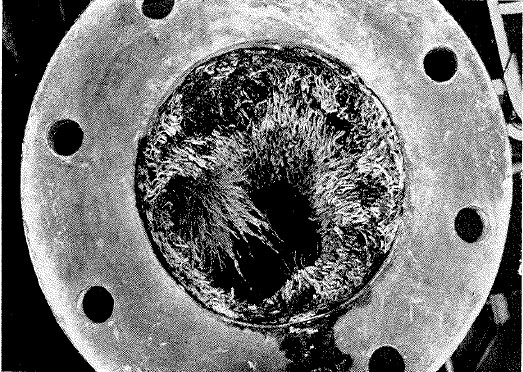
A 4" firemain, nearly plugged by tube worms
Fouling has been a problem since the dawn of sea travel. It slows ships, confuses sensors, and even makes hulls rust. The last century and a half has seen a great deal of work put into mitigating the problem, but it will undoubtedly be with us for as long as man goes to sea.2
1 A good illustration of the value of modern anti-fouling paint comes from the experience of HMS Illustrious, rushed to the South Atlantic just after the Falklands without antifouling paint. After 5 months in the River Tyne (heavily polluted and thus not a good place for fouling) and then 9 months in the South Atlantic, frictional resistance was 2.5 times the level it was for a clean ship. This corresponded to a 3 kt loss in speed, and when her bottom was cleaned, shaft power at low speeds fell by 80%. ⇑
2 For more than you could ever want to know about fouling, see this 1952 report on the subject. ⇑
Comments
Wow, those numbers are staggering.
Are submersible cleaner drones potentially part of the modern solution?