I've previously looked at the development of the shell fuze from the earliest days through WWII. But all of those were intended for use against surface targets, and during WWI, a new threat emerged, that of the airplane.
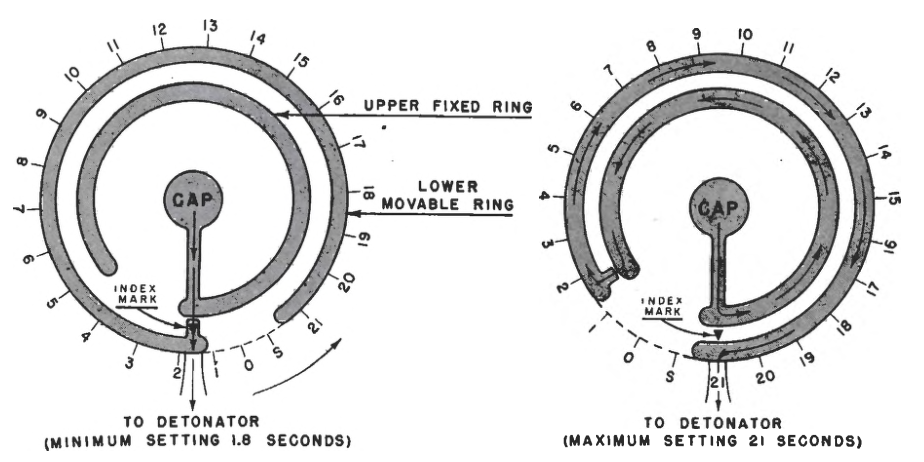
A powder time fuze's internals
This led to a reemergence of the time fuze, as the sky was very big and planes were small, and setting off the shell when it should be near the target was a lot more effective than hoping for a direct hit from heavy guns. This was surprisingly easy, as time fuze development had continued for use with shrapnel shells.1 The mechanism was surprisingly similar to some of the early time fuzes, but far easier to use. Essentially, the nose fuze had two horseshoes of delay composition which could rotate relative to each other, with a vent between them to allow the combustion to spread from one to another. To set, the operator (who was quickly replaced by a mechanical setting machine) merely rotated the nose section to the correct position, then loaded the shell into the gun, where the setback force would start the powder burning in the upper ring. Once it reaches the vent, it spreads to the lower ring, where it burns back towards the detonator. Minimum fuze time was generally limited for the safety of the crew (1.8 seconds was the US standard), but the use of setback to start the fuze train (even if a centrifugal safety mechanism would keep it from going off) meant that dropped time fuzes were particularly dangerous and generally needed to be thrown overboard immediately. Some early time fuzes also had a secondary impact detonator, although this seems to have become less common as dedicated AA time fuzes were developed.2
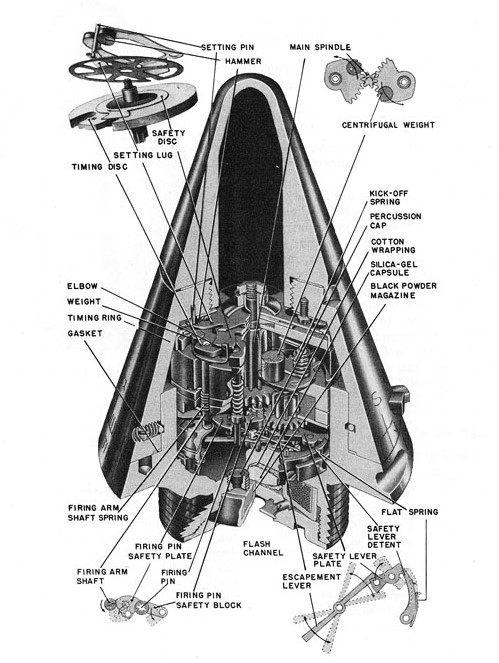
A mechanical time fuze
Unfortunately, service experience soon turned up a major problem with these time fuzes. The differences in air pressure experienced throughout their flight affected the burning rate of the delay element, with predictable results in an endeavor that involved shooting at a moving target in 4 dimensions. Navies attempted to solve this problem by replacing the powder fuzes with mechanical time fuzes, which used a clockwork mechanism that was safer (as it relied on centrifugal force to work) and theoretically more consistent in action. Operational tests seemed to show patterns only about 20% smaller, and the mechanical time fuze suffered a significantly higher dud rate early on, but the USN still made every effort to replace the powder fuzes in the years leading up to WWII.
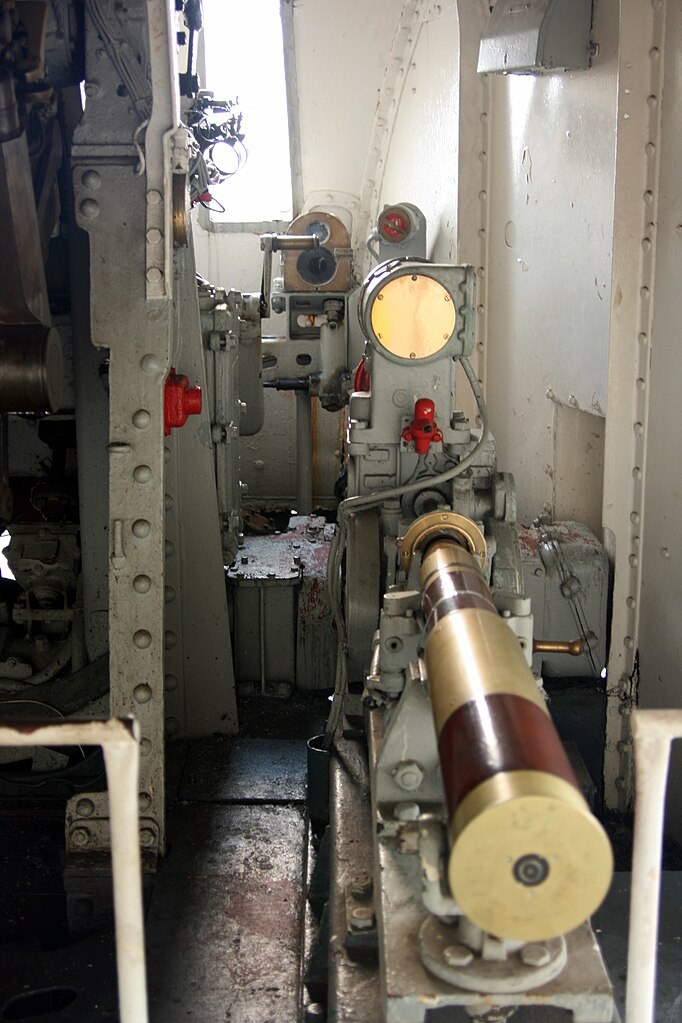
A 4" fuze setter on Belfast
Setting fuzes also complicated the loading cycle significantly. For most AA guns, the shell would go from the magazine or hoist to a separate fuze-setting machine near the gun. Initially, this would have a sailor estimating the necessary fuze time and inputting it manually, but this function was soon taken over by AA fire control systems. Once the shell was set, it would be loaded into the gun and fired. But this posed two problems. First, it slowed loading by adding an extra step, a problem that could be solved by integrating the fuze-setters into the hoists that brought shells up into a gun mount. The USN did this on the 5"/38s that armed the treaty battleships, with a significant improvement in rate of fire. But even that still meant there was a gap between the fuze being set and the gun being fired. The fuze-setter would try to compensate for this by setting the fuze to the required time based on when it should be fired, although a crew that was fast or slow would throw this off even if there were no changes to the solution during the loading interval.
All of this made AA fuzing a mess, and there were two possible solutions. First, what if all of this nonsense could be avoided by just making a shell that knew when to go off? Despite the massive technical challenges this posed, the US pulled it off during WWII, producing the VT (variable-time) or proximity fuze. Even the early models doubled the effectiveness of an AA shell, and it was widely used in the last two years of the war.
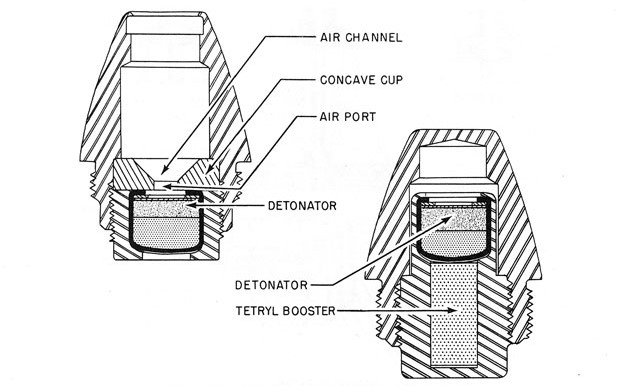
A 20mm fuze
Second, why not just shoot a bunch of smaller shells which could detonate on impact? Unfortunately, ballistics meant that this didn't work particularly well at long range, but at short range, small-caliber guns were very effective. Guns down to 20mm used explosive shells, although the volume constraints of smaller projectiles posed a special problem. The 40mm Bofors used a fairly conventional fuze, with a firing pin held by centrifugal safety pins striking a detonator housed in a weighted rotor that was moved into the correct position by centrifugal force. The 20mm, with a much smaller shell, had virtually no safety mechanisms whatsoever, relying instead on the shock of impact to set off the round. This posed a problem if the gun was fired with the muzzle cover on, so standard practice was to load the magazine with a couple of solid rounds on top. The shells of most small AA weapons also had a second fuze in the rear of the projectile, fired when the tracer compound, which made it possible for the gunner to see the projectile's flight path, burned out.3 This was intended to keep the shells from falling on friendly vessels, and was thought to have a useful deterrent effect on attacking pilots, who would be understandably reluctant to fly through shell bursts. A similar effect was expected from time-fuzed AA shells, and explains their continued use even when proximity fuzes were available in the last year of the war.
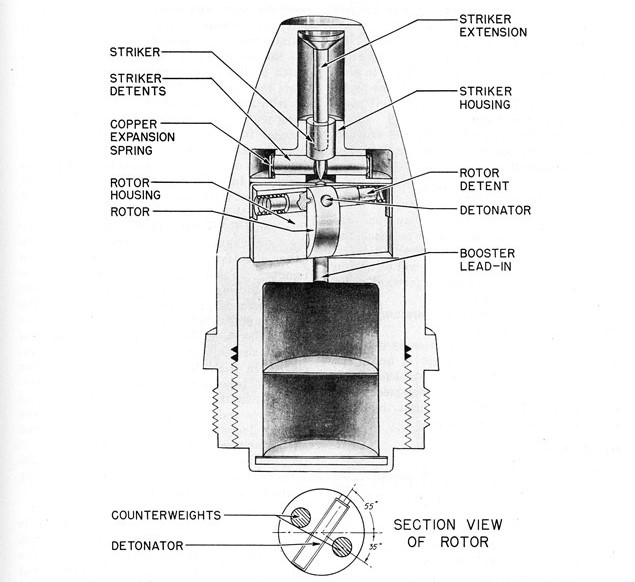
A 40mm fuze
Development of fuzes continued postwar, with electronics taking over from mechanical systems for smaller size and greater reliability. Proximity fuzes became more sophisticated, with a mix of radio, passive IR and laser systems seeing service in current shells. They also got smaller. For a long time, 3" was the minimum size for a viable VT fuze, but there are a number of 40mm proximity fuzes in use today. Proximity fuzes used against land targets are generally set so that they don't begin radiating until fairly late in the flight, to deny the enemy the chance to switch on countermeasures.
There have also been some exciting developments in recent years, with fuzes that can be programmed with more than just the time. A typical example can be set for either proximity (with slight variations depending on the type of target), time, or impact (immediate or delayed) modes immediately before firing. But there are more exotic types, like fuzes that also incorporate precision guidance kits, allowing an existing round to be guided, although this seems restricted to land-based artillery at the present, and the extremely interesting 35mm Millennium Gun. This fires a time-fuzed projectile that is composed of a few hundred tiny fragments, set to detonate ahead of the target and shred it. Uniquely, the fuze is set after the projectile is fired using an inductive device on the muzzle,4 which not only removes the problem of dead time, but also allows the gun to compensate for variations in muzzle velocity. And I'm sure that there are more exciting developments on the way that I don't know about.
1 While shrapnel was phased out at sea, it remained common on land. Amusingly, the British licensed their main shrapnel shell from Krupp, and had to pay significant licensing fees after WWI for fuzes they had fired at the Germans. ⇑
2 Also worth a brief mention are ignition fuzes, designed for payloads like starshells which burned rather than exploding. The principle of the mechanism was the same, but details were different to allow the contents of the shell to light instead of being blown up. ⇑
3 Many base fuzes for larger shells had space for tracers to be inserted, although these rarely destroyed the shell when they burned out. ⇑
4 For those who don't understand, electrical induction is basically magic. ⇑
Comments
This is fascinating, but also makes by head spin. It's amazing to me that they were able to get all this worked out reliably enough for wartime use at large scale.
There's an amusing story from Richard Feynman's book about how he worked briefly for the army designing fuses, but had to give up:
"The problem was to design a machine like the other one--what they called a director--but this time I thought the problem was easier, because the gunner would be following behind in another airplane at the same altitude. The gunner would set into my machine his altitude and an estimate of his distance behind the other airplane. My machine would automatically tilt the gun up at the correct angle and set the fuse. As director of this project, I would he making trips down to Aberdeen to get the firing tables. However, they already had some preliminary data.
I noticed that for most of the higher altitudes where these airplanes would be flying, there wasn't any data. So I called up to find out why there wasn't any data and it turned out that the fuses they were going to use were not clock fuses, but powder-train fuses, which didn't work at those altitudes-- they fizzled out in the thin air. I thought I only had to correct the air resistance at different altitudes. Instead, my job was to invent a machine that would make the shell explode at the right moment, when the fuse won't burn! I decided that was too hard for me and went back to Princeton."
Kind of amazing that this guy who later won a Nobel prize for physics would openly admit that the problem of proximity fuse timing in the air is just too hard for him and give up on it.