Military aircraft have to operate in a huge range of environments, from the deserts of the Middle East to the heat and humidity of the tropics to the cold of the high arctic. The obvious way to test these capabilities is to simply send airplanes out to these environments and see what breaks, but this is expensive and uncertain. Maybe there's a warm spell in Alaska this year, and the temperature doesn't get down to the point we're interested in testing at. To avoid this problem, the US Air Force sends its planes to Eglin Air Force Base in the Florida panhandle, where a hangar waits that can simulate almost any weather conditions on Earth.
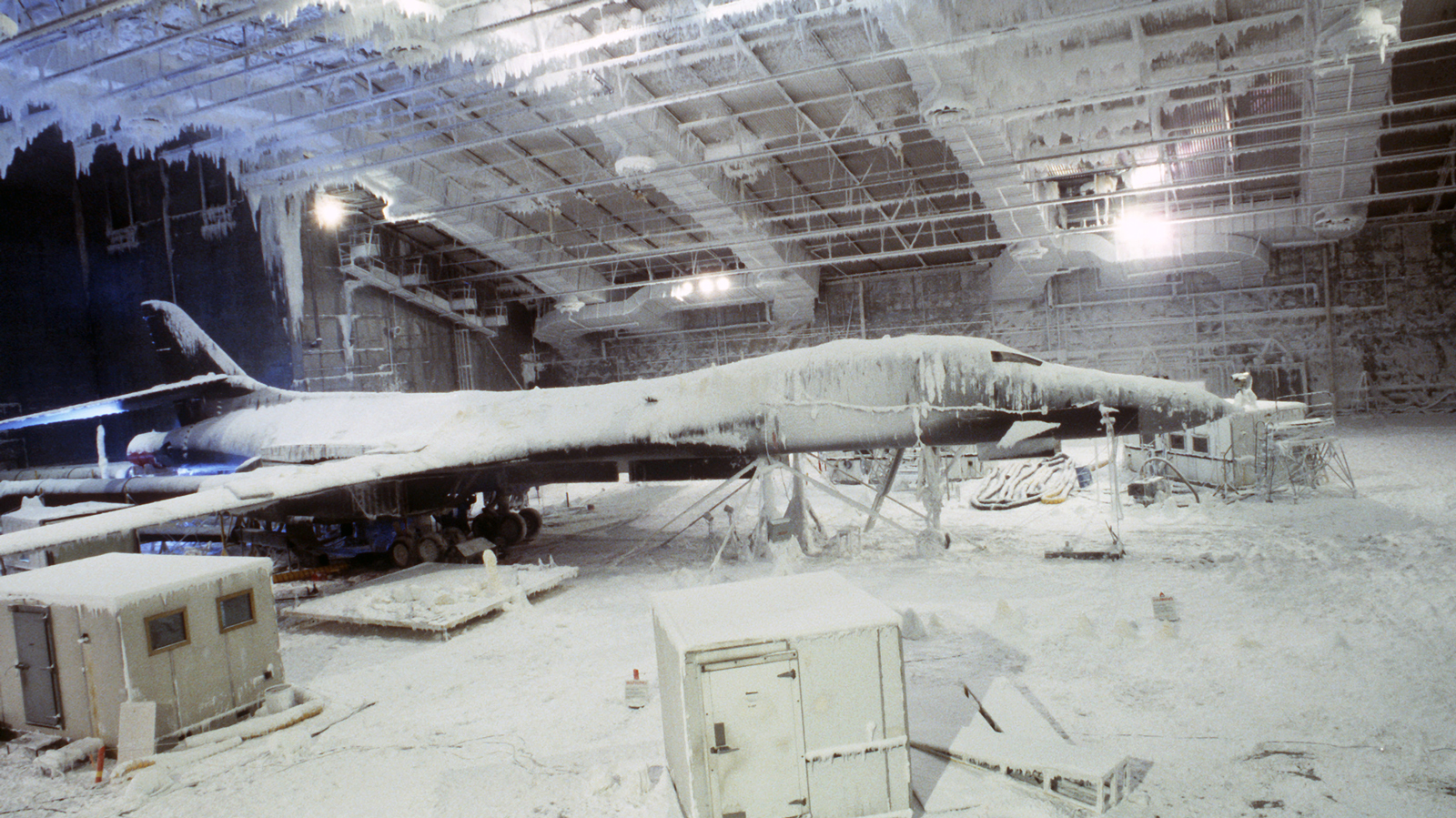
A B-1B undergoing cold-weather testing
The centerpiece of the McKinley Climatic Laboratory is the Main Test Chamber, a 55,000 square foot hangar capable of swallowing any aircraft in the US inventory and simulating virtually any weather conditions on Earth. The temperature can be set anywhere between -65°F and 165°F, and combined with high winds, torrential rains, fog, snow, and solar radiation. This is enough to reveal a wide range of problems in future aircraft, everything from landing gear that won't retract when very cold to poorly-designed access panels that leak when pounded with wind-blown rain.
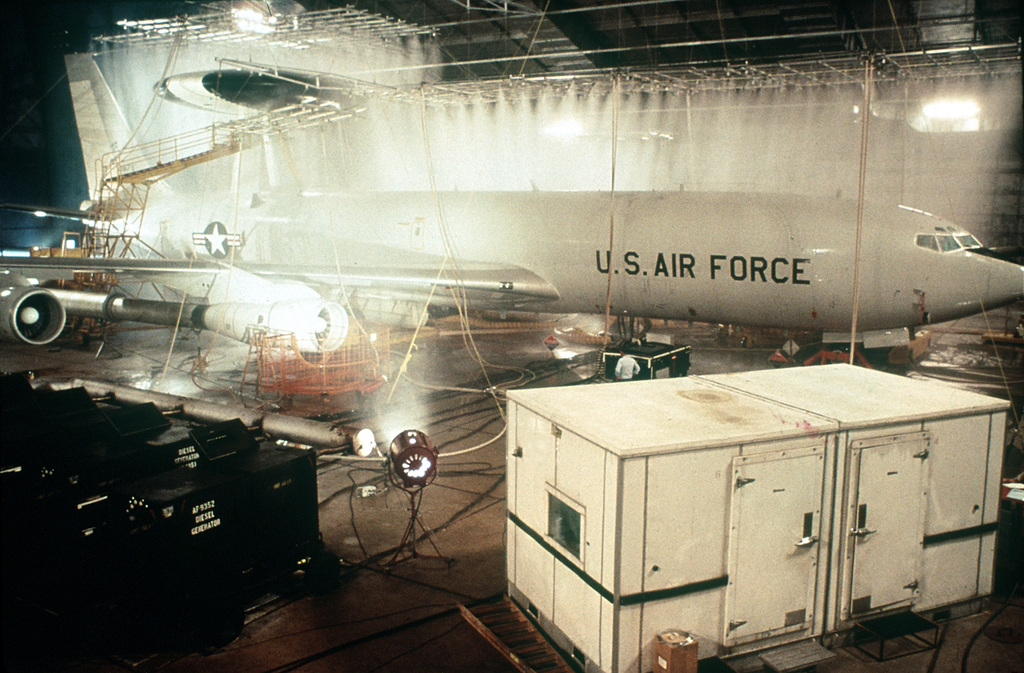
An E-3 Sentry during a rain test
The climate-control system that can turn 3 million cubic feet of hangar into whatever environment its operators want is simple enough in concept although deeply impressive in scale, but the real marvel is the air makeup system, which allows them to run the engines of aircraft in the chamber. Obviously, they can't simply turn the engines on and let them run. Not only would it quickly use up all of the oxygen in the chamber, but the temperature would rapidly rise and the volume of exhaust gasses would greatly exceed the volume of oxygen used, raising the pressure as well. The solution is to simply duct the exhaust out of the chamber, and then dump in air chilled or heated to the desired temperature at the same rate it is consumed by the engines. For smaller engines, the plant can cool the air as needed, but even McKinley's refrigeration plant can't keep up with, say, a 747's four massive engines. The solution? A 750,000-gallon tank of refrigerant, cooled to -100°F and ready to provide an hour or more of cold air to a large aircraft.
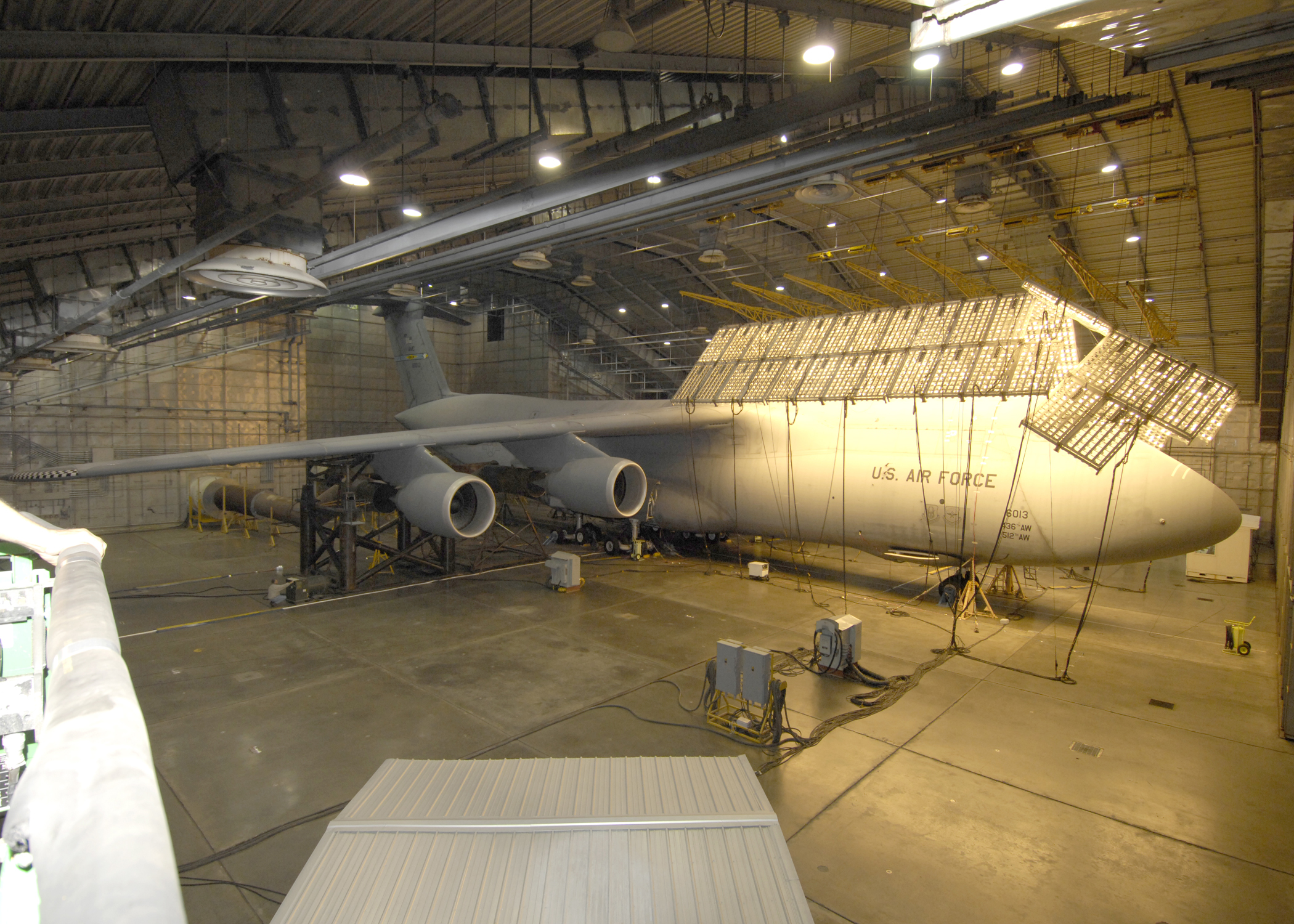
A C-5 Galaxy is baked
Nor does McKinley only test military aircraft. The facility is also available for hire by outside organizations, and most modern airliners have been tested there, with the exception of the A380, which can't fit through the doors. Other equipment that needs to withstand severe weather, everything from cars and trucks to tents and missiles, has also been subject to the mercies of the technicians there. Obviously, many of these don't need the full volume available in the main chamber, and these are generally tested in the Equipment Test Chamber, a space originally meant for testing engines independently from the aircraft. Over time, engine manufacturers got their own extreme-condition test cells, and today it's usually used for tests of military ground equipment and vehicles.
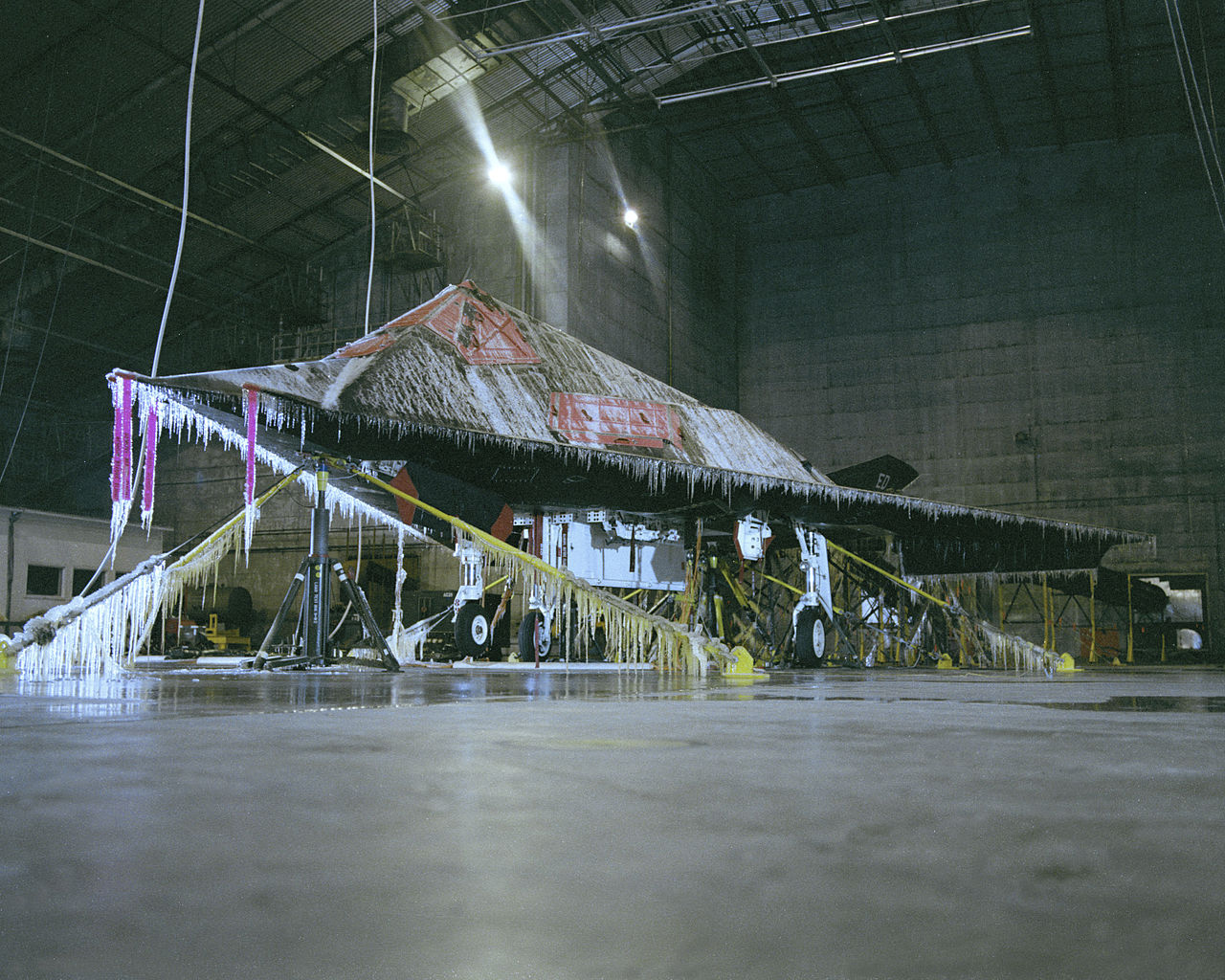
An icing test on an F-117
But even the main and equipment test chambers can't replicate everything, and a trio of specialized test chambers complete McKinley's arsenal. First is the Sun, Wind, Rain, and Dust Chamber. This is a small space capable of taking its contents from -80°F to 170°F, soaking them with 25 inches/hour of rain or sandblasting them with dust at 60 kts. The Salt Fog Chamber can replicate the corrosive conditions of the tropics with a special system designed to produce 100% humidity and a fog containing 5% sodium chloride. And to make sure that the low pressures of high altitude don't cause issues, the Altitude Chamber can take test articles up to a simulated 80,000' at temperatures between -80°F and 140°F.
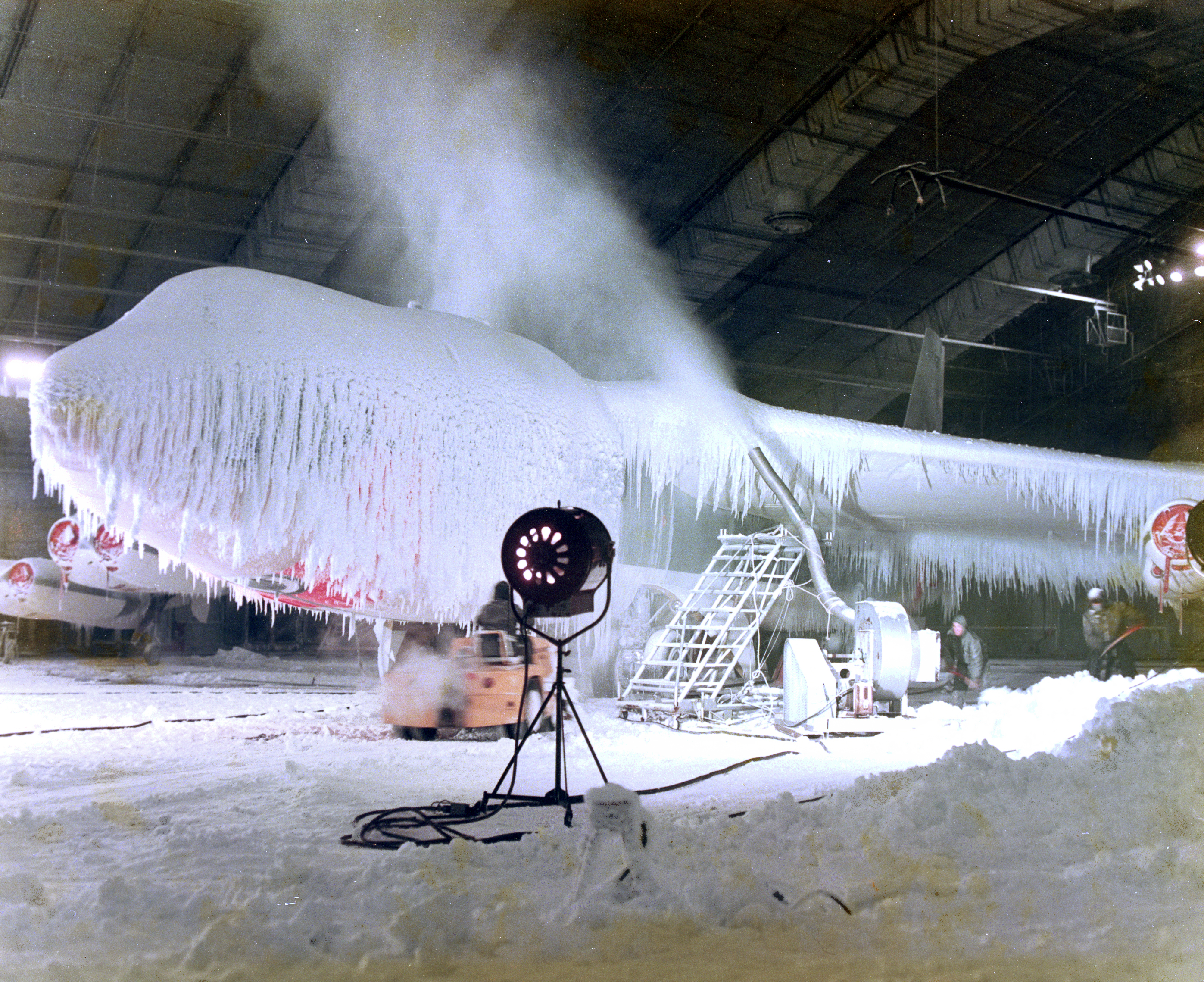
A snowstorm is generated for a B-52
Ultimately, the McKinley Climatic Laboratory is a marvel of engineering, one of the numerous facilities the US military has built to make sure that its weapons will do their job, whatever the conditions.
Comments
Great article Bean. Thanks for digging this up. I had no idea that they could run the engines in this hanger. That is really cool (no pun intended) how they can port the exhaust, pump in fresh air, and maintain the temperature.
I had heard this lab was well equipped but I had no idea that its range of capabilities was so great.
Do you happen to know if this is where they run fuel freezing tests?
Good stuff here--thanks again.
I'd guess fuel freeze testing is the sort of thing they do in lab machinery that chills a small sample. You could do it at somewhere like McKinley, but it's rather overkill and a poor use of resources. Chilling small samples is easy. Chilling an entire airplane is somewhat harder.
@Bean
I didn't do a good job posing my question. What I meant to ask was if they did any fuel in tank testing with the wings being cold soaked. I know on the Polar routes one occassionally has speed up by .01 or .02 Mach if the fuel temp drops below a present value--usually around -38C or so. I have always been curious how they determined how they could determine that they could count on the overall fuel temp increasing by this increased airspeed. Sure the heating of the wing's leading edge, but how did they go about testing it.
As we saw with BA flight 38 freezing fuel components require serious engineering focus. I once saw a technical paper from Airbus on low fuel temps and I found it absolutely fascinating. Obviously the military has done the leading research over the years in the field.
I'm not sure McKinley is going to be the place for that. I'm not sure you could do it except in flight. Presumably, you'd instrument the fuel and the skin of one of the flight test aircraft, and get the correlation from that. Moving air at high altitude is going to have very different heat transfer characteristics from still air at sea-level density.
Good point Bean. One of those areas where actual flight test seems to be the only/best way to determine performance.
I assume that for transport category aircraft Boeing collected reams of information and data in the late 50's forward from types such as the RC-135 which certainly had many hours in deeply cold air...
I'm pretty sure Boeing got no data at all off of the RC-135. The (minute) chance that the bad guys could learn something from it would almost certainly have been judged too great.
My guess is that somebody noticed it would be a problem and either the USAF or the NACA went out and did the basic research on the issue with whatever platform was handy. A Canberra, maybe. Once the basic shape of the problem is understood (things like the relationship between heat transfer rate, mach number, and air temperature/density) you really should only need an empirical coefficient for each type of airplane to make the equation work. Presumably, you calculate it from flight-test data.
But this is only a guess, and I don't really feel like digging deeper. If you want to run down the actual answer, the best place is undoubtedly NASA Technical Reports Server, which has a huge range of public-domain data on this kind of stuff.