During the 1960s, the world's shipping companies were in trouble. Their existing break-bulk cargo ships were proving uneconomical to load and unload as labor costs, particularly in developed countries, climbed, and ships spent over half their time sitting still while stevedores emptied and filled their holds. Something better would be needed, presumably a way to package cargo into larger containers which could be moved on and off the vessel relatively easily.
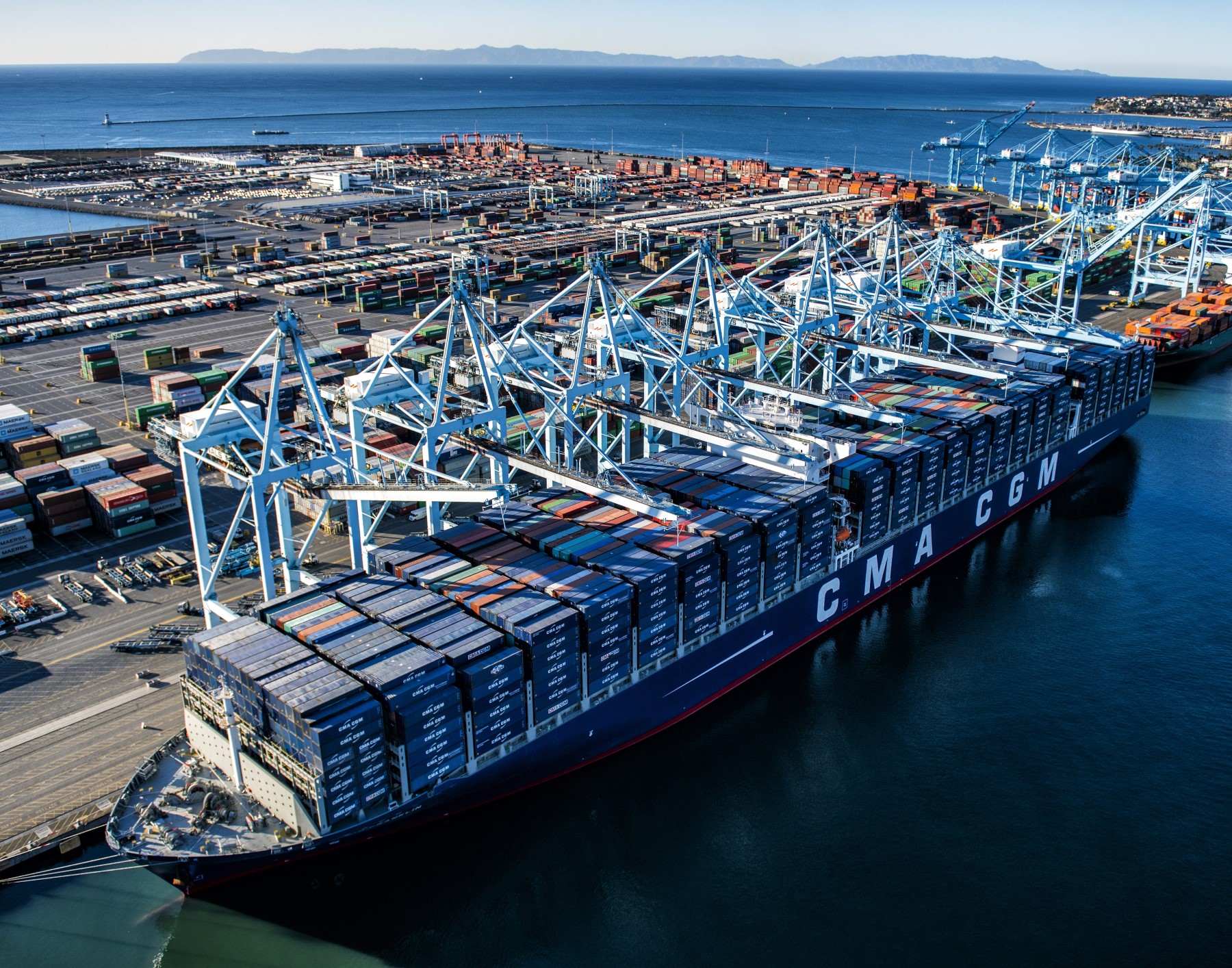
CMA CGM Benjamin Franklin, the largest container ship ever to dock in North America1
This wasn't a completely new idea. In fact, its roots stretched back over a century, to the early train ferries, designed to bridge bodies of water too wide for bridges. Fully-loaded rail cars would be brought aboard on internal tracks and then shuttled across to the other side. Much the same was done during WWII, when LSTs were filled with fully-loaded trucks, which would simply be driven off on the beach at the far end. However, this kind of loading was rather inefficient, with an LST able to carry only a quarter of what it could if loaded with bulk cargo. During the Bismarcks campaign, the sacrifice in cargo was unacceptable, and a compromise was found in the form of loading the LST with trailers, which could carry more cargo than trucks, but still be unloaded quickly.
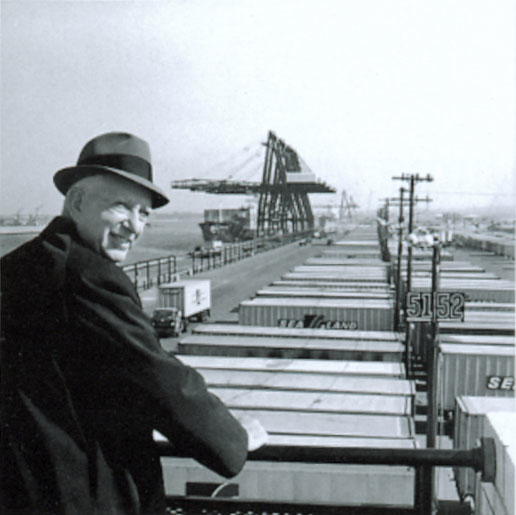
Malcom McLean
Postwar, ro-ro (roll on/roll off) service began with surplus LSTs, and while they worked reasonably well for short routes like the English Channel, space utilization problems made them uneconomical for longer routes. To solve this problem, Malcom McLean, an American trucking magnate, came up with the idea of detaching the boxes from his trailers and loading them aboard a ship via cranes. The first tests were carried out in 1955, with an oil tanker modified to carry 58 containers in addition to its normal liquid cargo between New Jersey and Houston. The handling costs fell from $5.38/ton for break-bulk cargo to only 16 cents/ton for containers, and McLean quickly began to expand his operations with pure container ships.
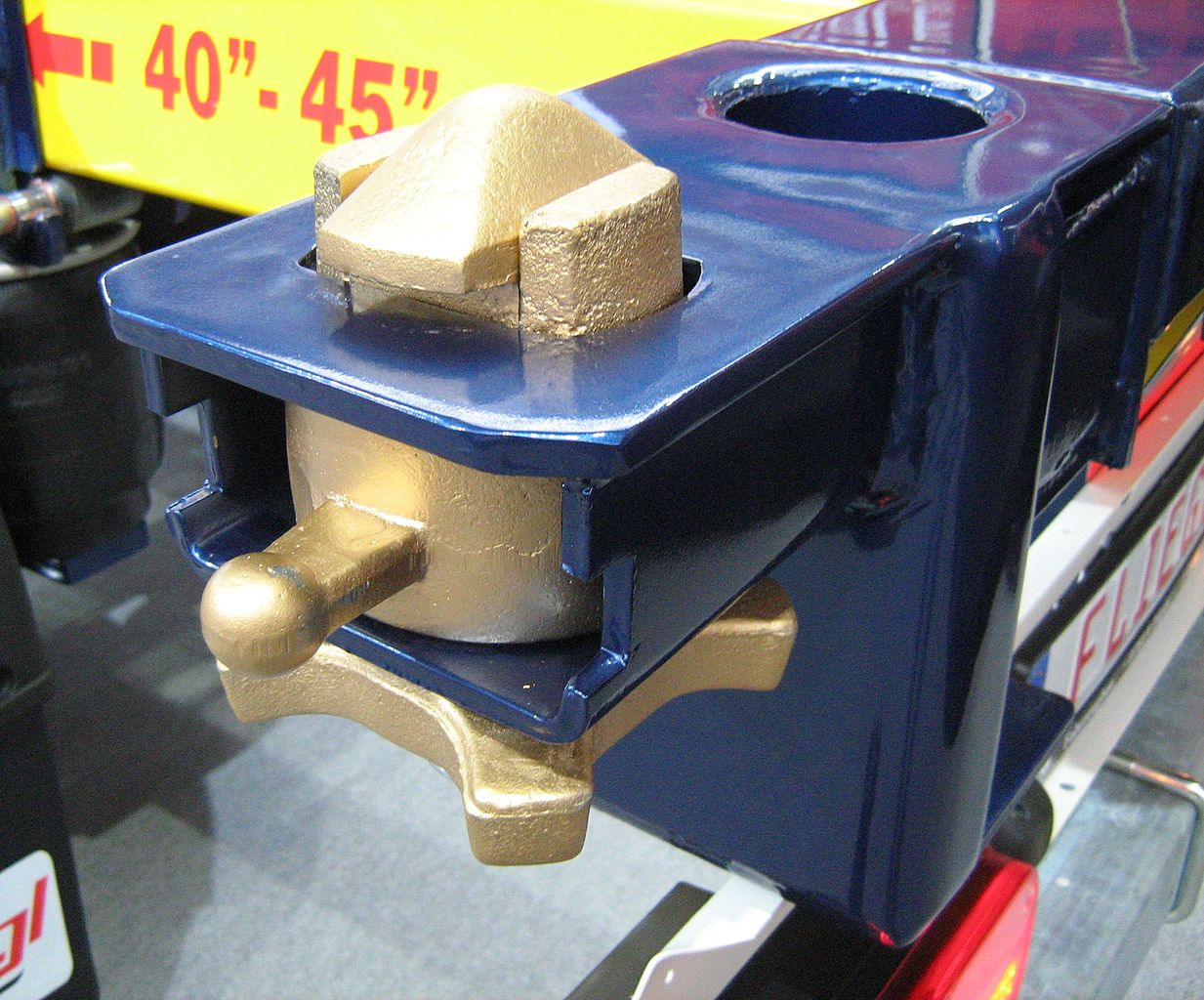
A Twistlock
During the late 50s, McLean and engineer Keith Tantlinger worked to improve the containers they were using, and soon developed the modern intermodal shipping container. 8' wide and 8'6" high to comply with American laws regarding road transport, these steel containers are usually either 20' or 40' long, although other lengths do see some service. A 40' container, which makes up about 70% of the global inventory, can carry about seven times the weight of the container in cargo, and can be stacked up to 9 deep, secured to a ship, train, or truck with standardized twistlocks. Besides allowing much easier handling at ports, the sturdy steel boxes also greatly reduced the risk of cargo theft and damage, and have found a massive variety of other uses as well. McLean licensed his patents royalty-free to the International Standards Organization in 1961, allowing easy development of a truly global container pool.2 Today, the total global container pool is around 34 million TEU.3
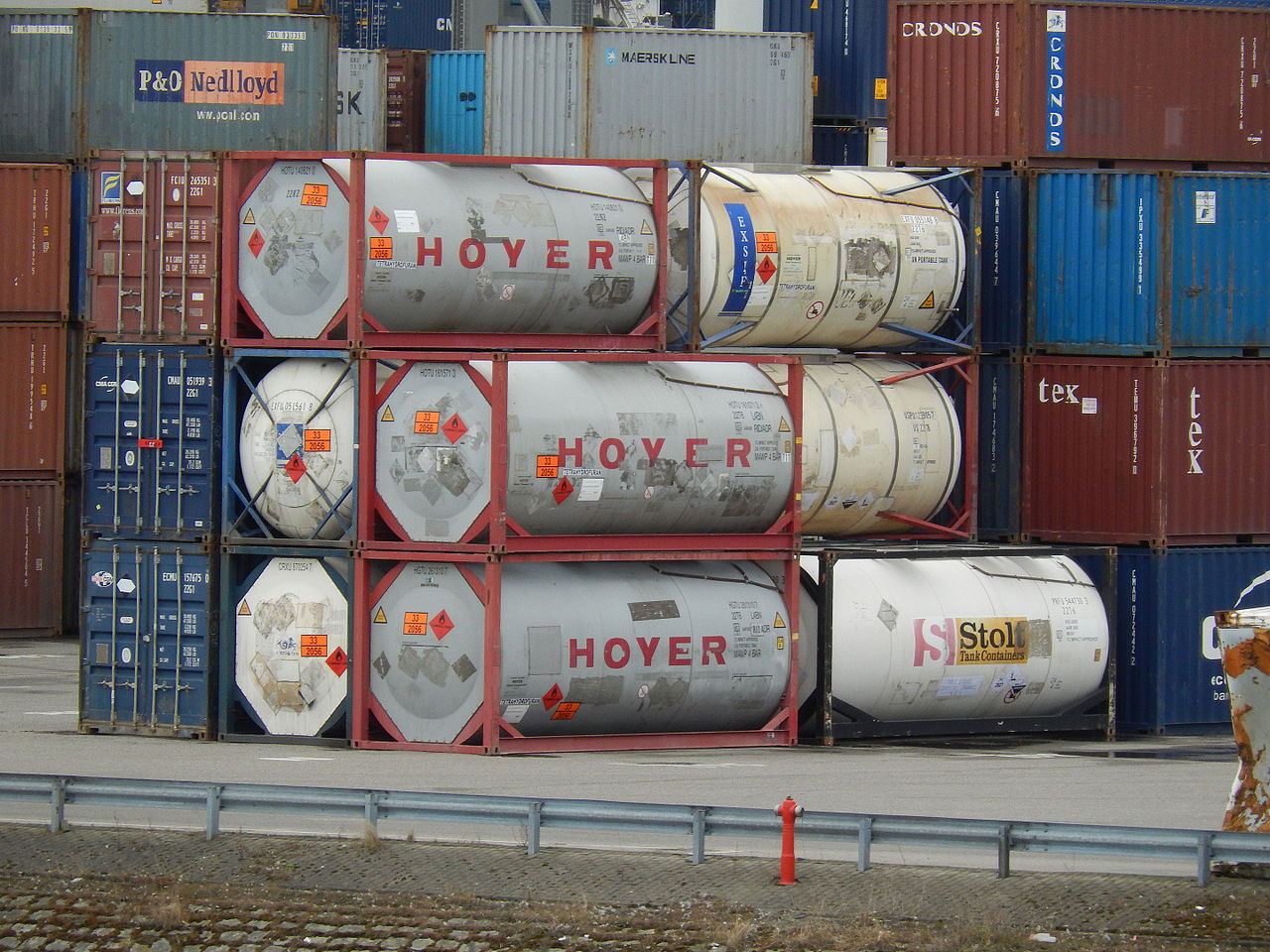
Tank containers stacked with standard containers
The vast majority of these are standard dry cargo (box) containers, although even some of these are specialized, "high cube" models which are 9'6" tall,4 and are usually used for bulky cargoes. But the basic format has been used as the basis for a bewildering variety of containers for specialized cargoes. Some have removable roofs for cargo that needs to come in from above, while others are designed to carry bulk cargoes like coal and grain, which are essentially poured in and out, removing the need for conventional doors. Temperature-sensitive cargoes are often transported in "reefer" containers, powered by the ship. Large cargoes that wouldn't fit in a normal container can be tied down on "flats" and hoisted aboard, with space left around them to accommodate the oversize cargo.
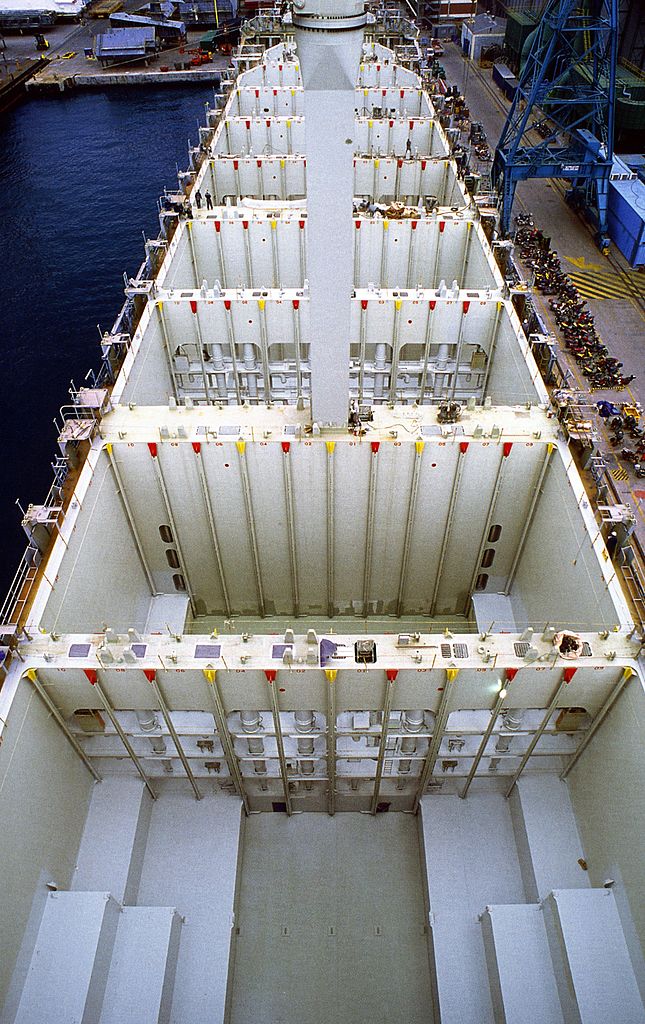
The cellular hold of a container ship
Oceanic container services began in earnest in the late 60s, with many WWII-era tankers converted to carry 500 or so TEUs. But the massive reduction in handling cost meant that the world's shipyards were soon full of orders for purpose-built ships carrying up to 2,000 TEU. Most of these used the so-called "cellular" system, a series of guides built into the holds under the deck that could accommodate up to 9 containers deep. Hatch covers would then be put in place, and another set of containers 5 deep would be stacked on top of them, locked together with twistlocks. Special care was required during load planning, as the heaviest containers had to go at the bottom to maintain stability. Containers also required developments in the legal environment of shipping. New rules for insurance, inspection, and customs were required to allow containers to move freely across national boundaries, and new ports had to be built to handle the containers.
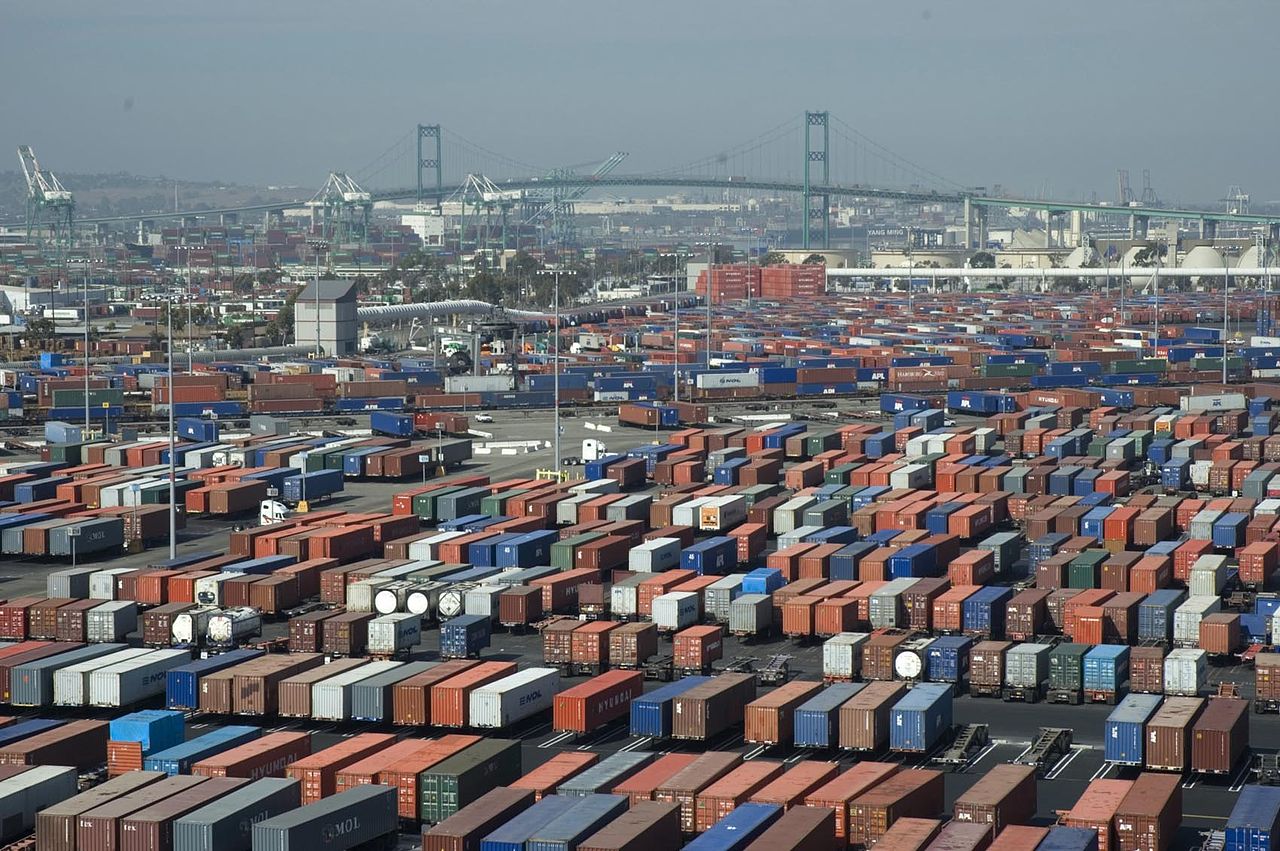
Containers wait on trailers at the Port of Long Beach
These ports were emblematic of the way that the container changed the world of maritime shipping. Instead of being in the heart of major cities, where thousands of dockworkers earned their livelihoods from them and crews from all over the world took shore leave, they were in remote areas where land was cheap. They were equipped with cranes, some able to handle a container a minute, which could often see a ship back on the way in a matter of hours. These combined to limit shore leave, destroying the cosmopolitan atmosphere that had defined major ports since Antiquity.
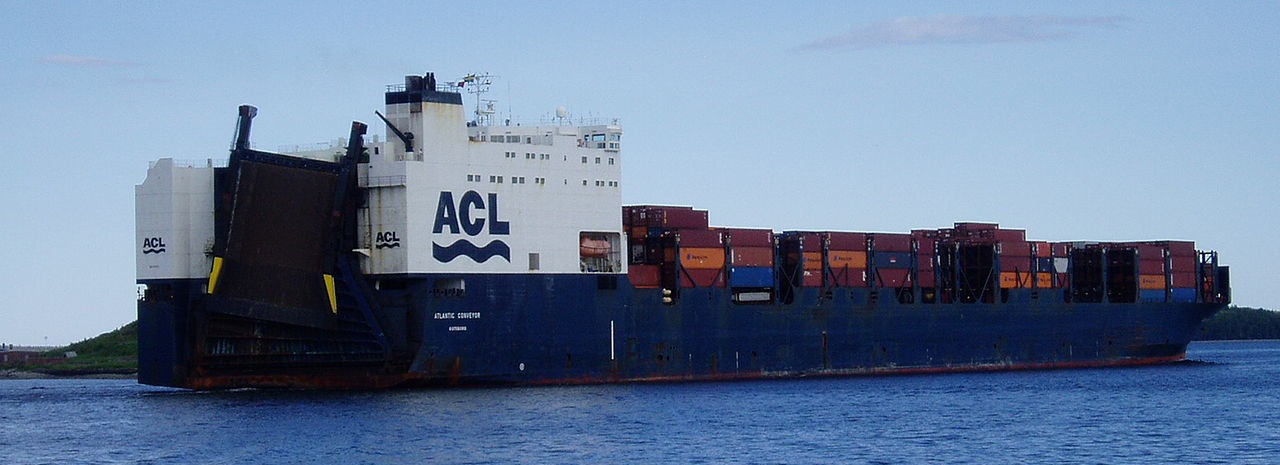
Container/Ro-Ro hybrid ship Atlantic Conveyor, showing her stern ramp for vehicles5
Another drawback of these ports was their expense. For a major industrial economy, they were obviously worthwhile, but for developing nations, the infrastructure was seen as unaffordable, and several solutions were proposed.6 The most common was the ro-ro ship, loaded with either trucks or separate trailers and requiring only a ramp to discharge its cargo. Some even suggested that it would ultimately prove more efficient than containers, and some companies built ro-ro ships for the North Atlantic run, such as the ill-fated Atlantic Conveyor, focusing on carrying cars, cargoes like forest products, and heavy equipment that couldn't fit on container ships. These were killed off by issues of handling cost and competition from more specialized ships, while developing nations began to invest in port facilities, and the cargo-carrying Ro-Ro faded in popularity, except with militaries who might have to unload in extremely primitive conditions.
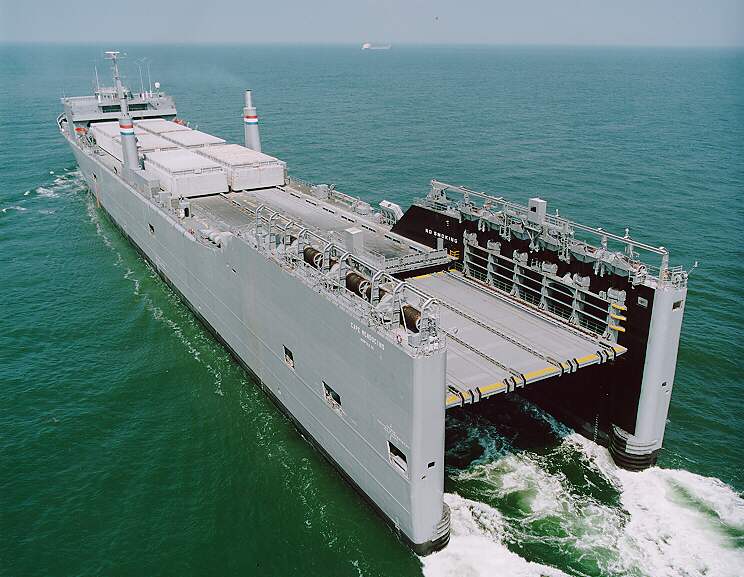
LASH Ship Doctor Lykes, showing her stern elevator
Another competitor to the container was the so-called LASH (Lighter Aboard SHip). This was a system developed when someone noticed that a lot of cargo was being transported down the Mississippi River in barges, then loaded onto ships in New Orleans and carried to places like Rotterdam, where it was then loaded onto barges that were towed up the Rhine. Why not cut out the middleman, and simply load a standardized barge onto a ship for the transatlantic journey? The original LASH ships were fitted with a crane which could lift the 460-ton barges onboard and stack them in the hold, while the related SEE BEE system used a large lift at the stern to carry bigger barges to deck level, then slide them on rails forward to their eventual destination. Ultimately, the overhead of dealing with the barges proved too large, and most of the remaining ships ended up in the hands of the US military, who are very concerned about operating in areas with insufficient infrastructure. Today, LASH is primarily remembered for the starring role it played in Tom Clancy's Red Storm Rising.
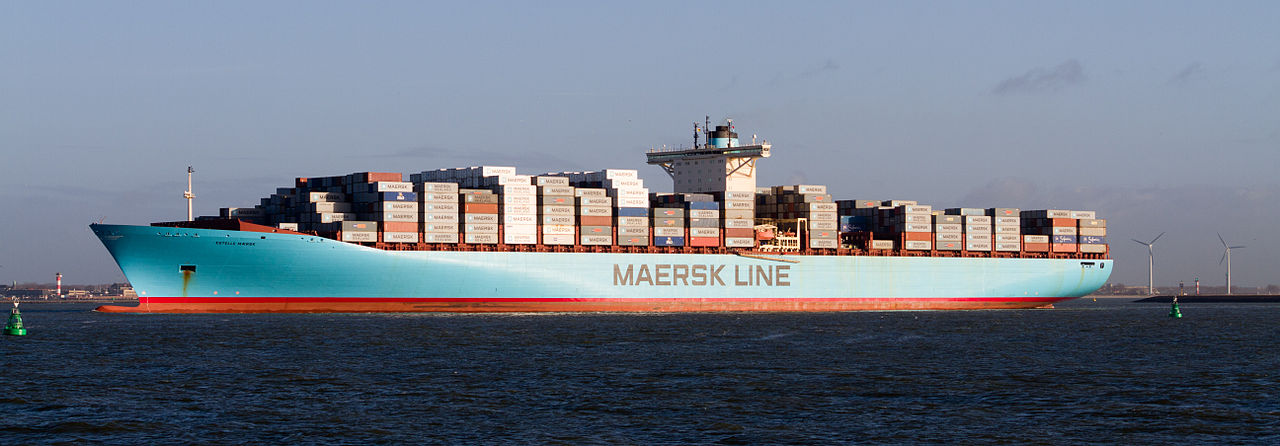
Estelle Maersk, one of the Maersk E class
The container market was relatively stagnant during the 1970s, but as the aftermath of the oil crisis faded and the world economy recovered, container ships began to grow, with the largest vessels passing 3000 TEU in 1981, and vessels beginning to reach the limits of the Panama Canal. By the late 80s, the top end had grown 50%, as shipping lines focused on the major routes across the North Atlantic and from the Far East to North America or Europe, none of which required the use of the Panama Canal. The next decade saw another doubling of ship size, and the first container ship of 10,000 TEUs, Gjertrud Maersk, was launched in 2005, eclipsed almost immediately by Maersk's E class, eight ships of 14,770 TEU each, the first of which entered service the next year. To cope with rising oil prices, Maersk followed these with the even larger Triple E class, which were a few knots slower, but could carry 18,340 TEU between Europe and the Far East. 31 of these vessels are now in service, although their size record was quickly snatched by even larger competitors. The 20,000 TEU limit was breached in 2017, and MSC's Gulsun, the largest container ship at the time of writing, has a capacity of 23,756 TEUs.
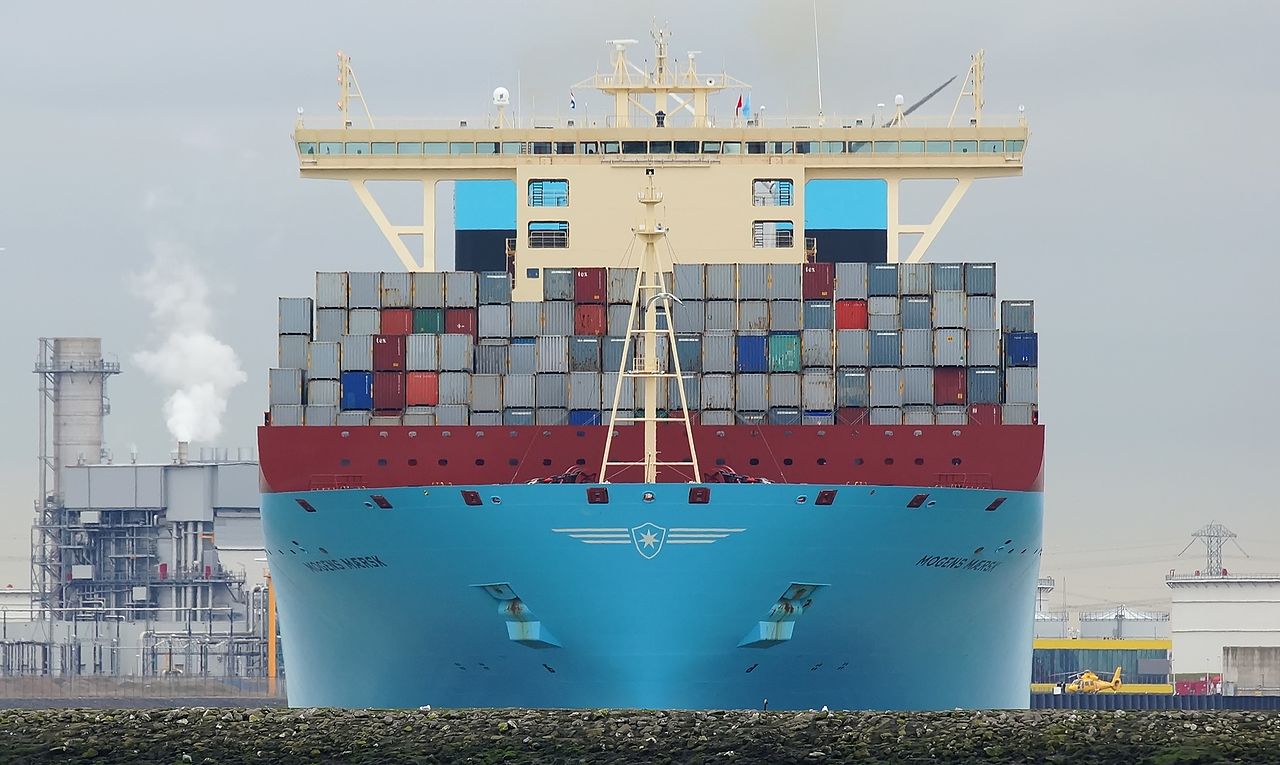
Mogens Maersk a Triple E
This frantic growth in ships had lead to an equally dramatic decline in shipping rates. Modern cargo moves far more smoothly around the world than has previously been possible, at least so long as someone doesn't go and block a major trade route. As recently as the 50s, shipping costs often exceeded import duties as a percentage of the value of the cargo. Today, they're so low that they can usually be neglected for an initial analysis, which has allowed global supply chains to develop. The speed and certainty of container shipping has allowed other innovations like just-in-time ordering for manufacturers, who no longer need to pay inventory costs to cover the risk of a cargo getting stuck somewhere along the way. Despite some hiccups, this system proved remarkably resilient even in the face of the pandemic, and looks set to continue into the future.
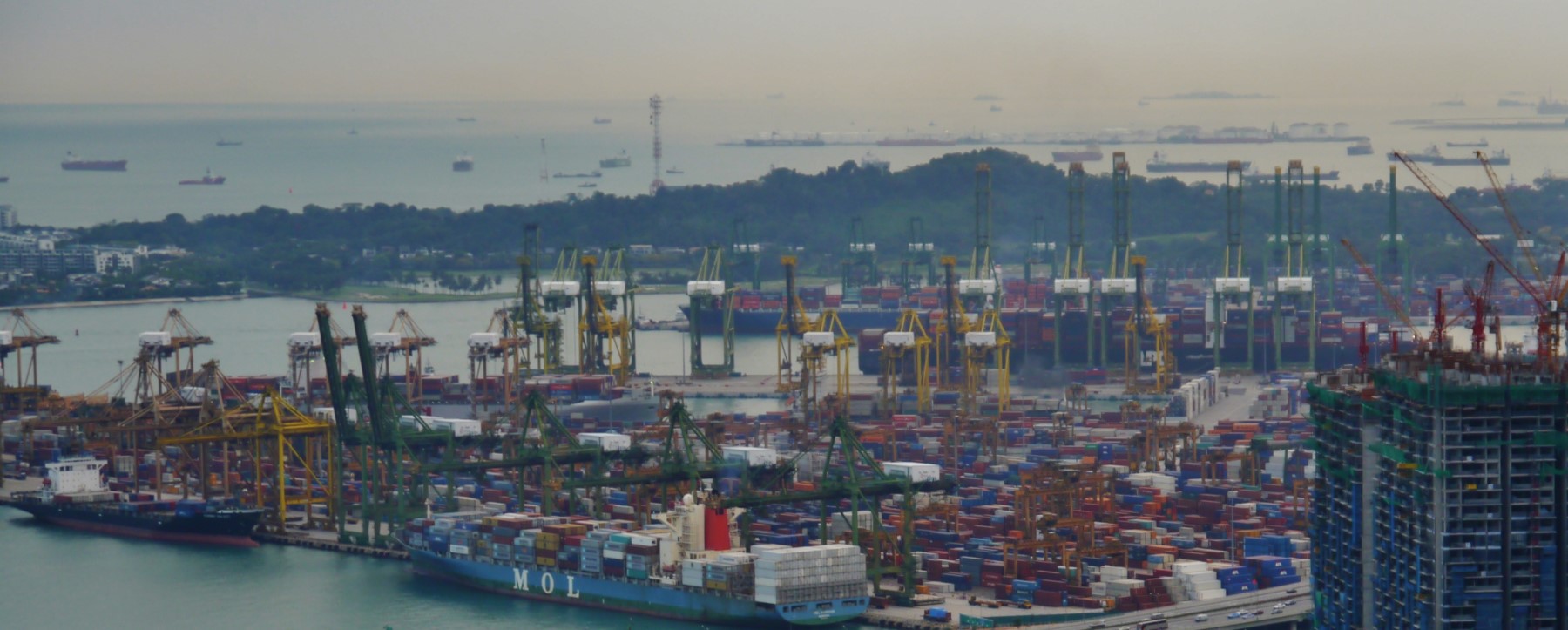
The Port of Singapore
Today, shipping is an incredibly efficient industry, with 1.6 million seafarers, less than .02% of the world's population, responsible for transporting 90% of all cargo. The world's busiest container port, Singapore, handled 37.2 million TEUs in 2019,7 mostly goods going from factories in East Asia to destinations in Europe, at an average price of something like $1,600 port-to-port for a 40' container, capable of carrying 28 tons.8 As a means of moving goods around, the container is astonishingly cheap, and has been responsible, probably as much as any other invention, for creating the globalized world we live in today.
1 Photo courtesy of the Port of Los Angeles. ⇑
2 If I may be allowed a soapbox for a moment, this is probably what McLean should be remembered for. Containerization had been toyed with in one form or another for many years before he showed up, but developing a good container and then making it free for everyone to use greatly aided adoption of the technology, which otherwise would have been hindered as each shipping line tried to develop its own container. ⇑
3 Twenty-foot Equivalent Units, the standard measure of container capacity. Most containers are 40' instead of 20', so this means that there are probably something like 18 million containers in use today, but it's easy enough to swap out a single 40' for two 20', so TEUs it is. ⇑
4 Improvements in trailer design mean that these can now be transported on American roads, but the 8'6" designs are still the standard. ⇑
5 This is not the vessel lost in the Falklands, but her replacement. ⇑
6 Some container ships do have cranes onboard to handle containers. These are known as "geared" ships, but only the very smallest container ships, which transport containers to and from very small ports, are routinely geared. ⇑
7 Most sources say this is something like 10 or 20% of the world's containers, although it's also close to the best number I have for the total stock. Figures on this stuff are surprisingly hard to figure out. ⇑
Comments
Great series Bean. Very glad you tucked into this as logistics on this scale is simply fascinating. Your last sentence about containerized shipping being the true key to globalization sums it up briliantly. I had no idea that rates were as low as $1,600 for a forty footer to a destination across the world.
Stop in at a FedEx office in Boston with 16 medium sized boxes to be shipped to San Diego and you might need to drop the same amount of cash. Granted the time factor but still...
Once in Bremen, Germany I got to watch up close as BMW crews unloaded autos that had been made in South Carolina. An absolute master display in efficient movement. I can't remember how exactly long it took, but the process moved along full apace.
$1600 is actually the expensive end of the run. Containers going the other way are much cheaper, because of the way manufactured goods flow. (Of course, prices were as of a month ago, and goodness knows what they're like today.) Car carriers are a different thing, but pretty much the whole of international shipping is run to an incredible degree of efficiency.
Looks like the 37M TEU number for Singapore is container traffic, so it's not so odd that it's close to total container stock. Though the numbers I'm finding for global container traffic are in the ~800M TEU range, which gives Singapore a ~5% share.
Maybe 10-20% of containers visit Singapore at least once each year, and most of them visit multiple times?
The problem is dwell time. I believe a typical ship's passage China>Singapore>Europe is at least six weeks, so you're only able to get maybe 9 one-way trips a year. Less, realistically, because you need to load and unload the containers themselves. So it can't just be 10% of containers go through Singapore more than once. I didn't want to spend a bunch of time chasing down statistics on this, because it's a fairly peripheral point.
I suspect a lot of the raw numbers for Singapore are relatively local routes. Going to Singapore from Shanghai or Calcutta or Jakarta or Hanoi isn't going to be the majority of the ton-miles, but it'll likely be the great majority of the container count. And those routes can be done a lot more than nine times a year.
You do realize that there's no such thing as the International Standards Organization?
I'm going to blame the French for this one. I assumed ISO was an acronym, not a standardized designator.
The rule of thumb I use when calculating shipping costs is that to get a pair of jeans from a warehouse in Guangzhou, to a warehouse in Sydney, was 6 cents (Australian, so maybe 5 cents US).
Almost nothing, nothing at all in the purchase of those jeans was as cheap as the transport. It costs more money for the retailer to ring the sale up on the cash register. It certainly cost more money to take the jeans from the Sydney warehouse and put them on the display rack in the Sydney store.
Of those 6 cents, maybe 2 cents were fuel costs. So a doubling of the price of oil means... a $100 pair of jeans is now $100.02.
Two things that Wikipedia glosses over are how port container handling infrastructure developed, and how the longshoreman's union didn't put a stop to it.
It sounds like Malcom started by building his own handling facilities, with containers spreading through specific high-demand-low-union routes?