At the end of WWII, the steam turbine was the standard means of powering large warships, turning propellers with reliability and economy. Today, steam propulsion all but gone from the world's oceans, and while large warships are powered by turbines, the turbines in question are turned not by steam, but by combustion gasses.
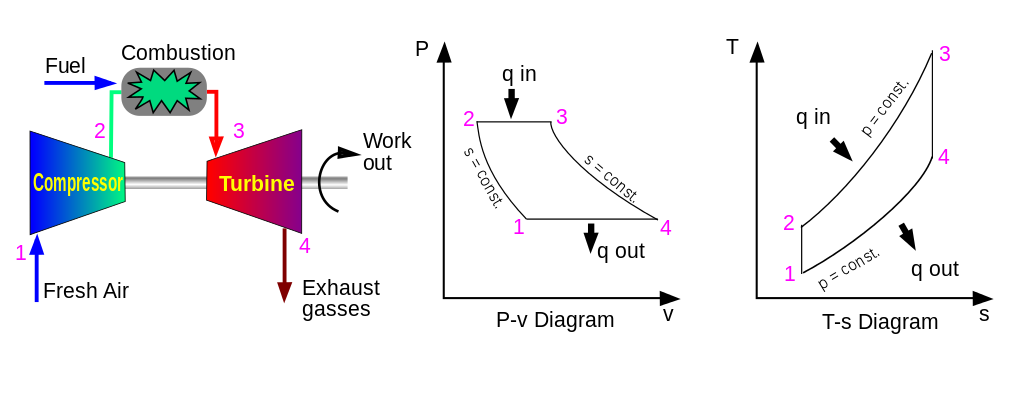
A turbine is, at its heart, a very simple machine, one that takes high-energy fluid and extracts energy from it, producing lower-energy fluid and rotary motion. A wide variety of fluids can be used, ranging from water (in hydroelectric dams and obviously of little interest in warship propulsion) to steam to the combustion gasses produced by burning jet fuel and air at high pressure.1 The last is known as a gas turbine, and it propels not only warships but also likely the last airplane you flew in.
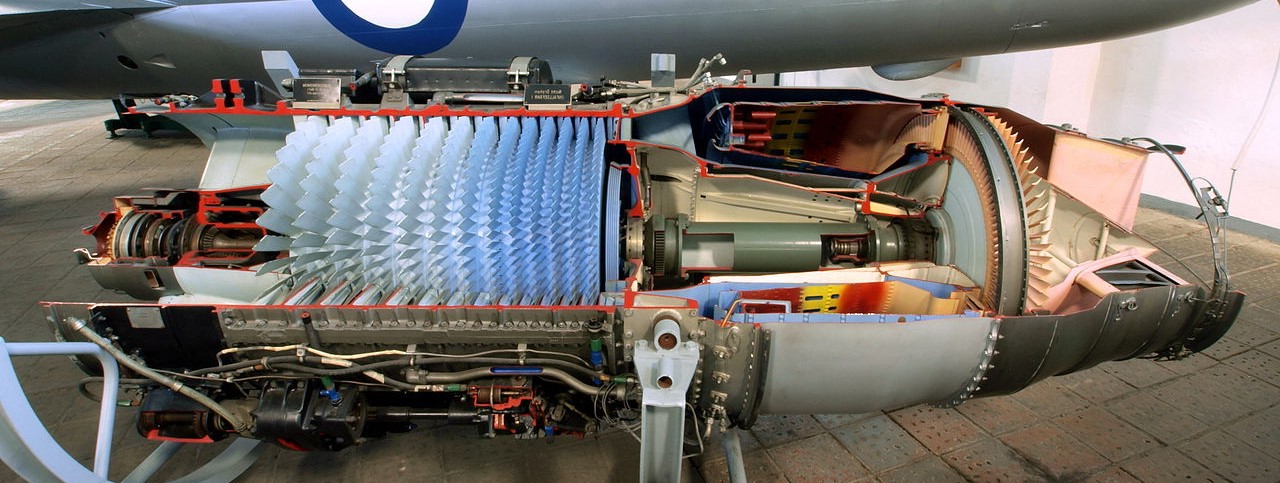
The turbine of a jet engine
The basic cycle of a gas turbine is very simple. Air is drawn into the compressor, so called because it compresses the air using spinning rotor blades interspersed with stationary stator blades, with each set known as a stage. A lot of stages are required because the air would rather not be compressed, and if it gets squeezed too hard too quickly, then it simply goes backwards and bad things happen. To ensure smooth operation over a wide variety of conditions, some of the stator vanes can be swiveled to optimize the airflow at low power. When the air is nice and compressed (say 20 to 1) the fuel gets injected, and then ignited. This adds a bunch of energy to the gas, which is then sent through a turbine which turns the compressor. This turbine is only a couple of stages, because it's taking energy out instead of putting it in, and because a higher turbine temperature means a more efficient engine, the blades are made out of the most temperature-resistant materials possible, and cooled with extra air from ahead of the combuster which is bled through tiny holes in each blade.
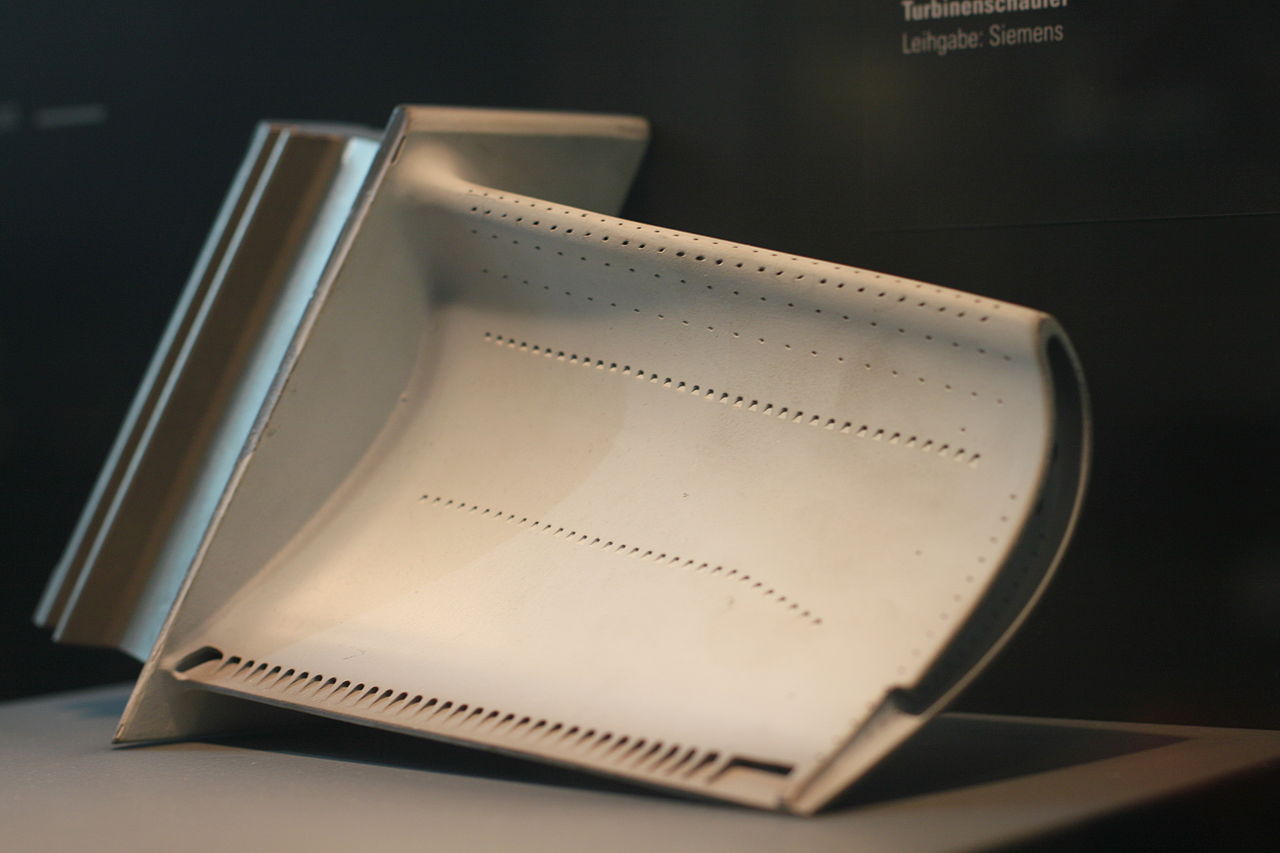
Cooling holes in a turbine blade
But that turbine only takes out about two-thirds of the energy from the gas, which still leaves quite a bit to use for other purposes. We could, for instance, stick a nozzle on the back of the assembly to channel the gas out at high speed, and call it a jet engine. But while those are extremely useful in the right circumstances, we're trying to propel a boat, and it's not a great choice for that. So instead, we'll run it into another turbine, which will take out more of the energy, and give it to us in the form of a spinning shaft. With a gearbox to take this from the several thousand rpm we get it at to a more reasonable speed for propellers, it will do nicely to move a warship along, and we can simply dump the exhaust gas overboard.
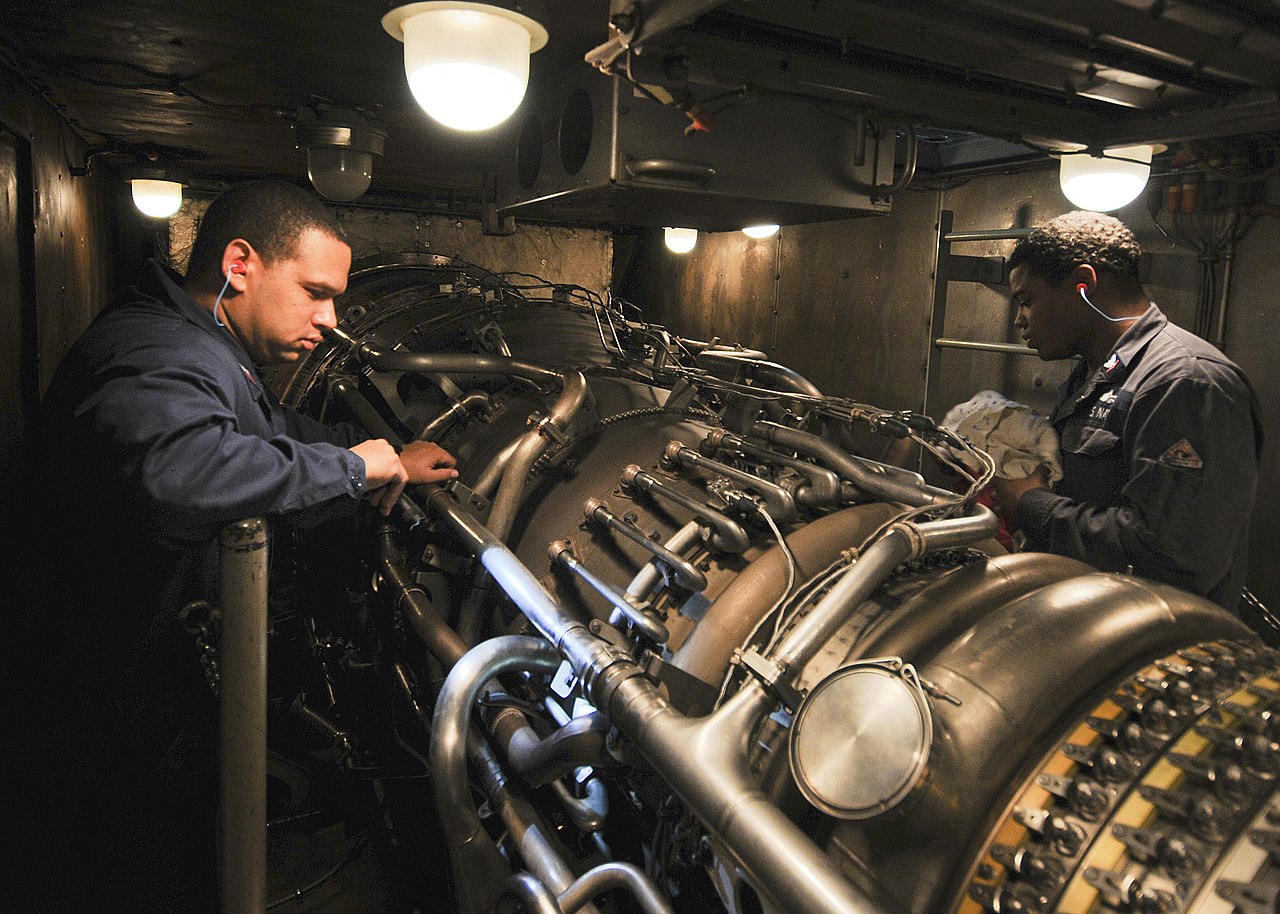
Sailors aboard cruiser Anzio work on an LM2500
The result is a compact, very powerful and largely vibration-free means of propelling ships, which was also able to benefit from the research being poured into jet engines. Even today, all major marine gas turbines are derived from aircraft engines. The GE LM2500, which powers both the Ticonderoga and Arleigh Burke classes, was derived from the CF6 turbofan that powers a number of airliners, and Rolls-Royce has turned the Trent 800, used on the Boeing 777, into the MT30, plant of choice for the Zumwalts and Queen Elizabeths. Unfortunately, this close relationship with the jet engine industry does have its downsides. A naval architect has essentially a fixed set of engines to choose from, and can't easily ask for 10% more power should he find himself in need of it. He'll have to either install more engines or go to steam or diesel.
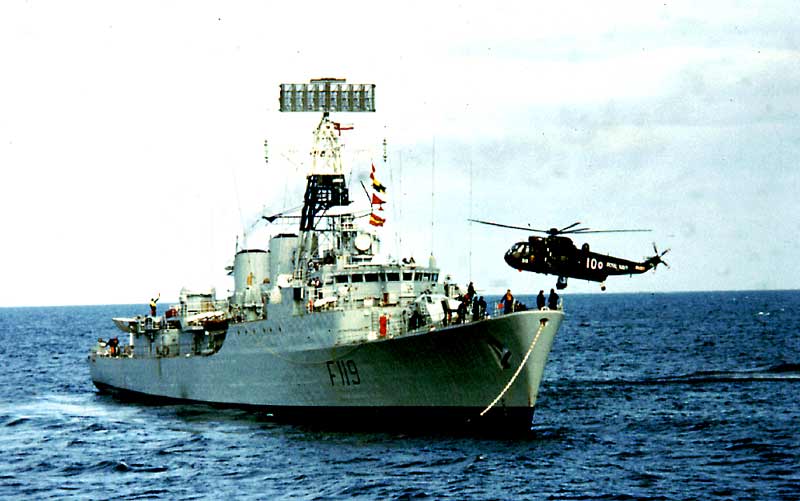
HMS Eskimo, one of the earliest large gas turbine warships
The gas turbine's advantages (which also include vastly better throttle response, in seconds rather than minutes or hours for steam) are balanced by a set of disadvantages. Early gas turbines were as unreliable as the jet engines that spawned them, and while 100 hours between overhauls seems like a lot for an airplane, it's precious little for a ship, and they were primarily used as boost plants for top speed, with steam or diesel for cruising, a subject I cover in another post. Today, developments in engine technology mean that gas turbines are not only reliable but also extremely low-maintenance. Provided the air coming in is dry and free of debris (which means intakes high in the ship and elaborate ducts and filters to make sure it's clean and flowing smoothly), it will last for thousands of hours with minimal care. When the time comes, simply hoist it out and put in a new one, then send the old unit off for an overhaul. HMS Invincible even carried out the procedure at sea during the Falklands War.
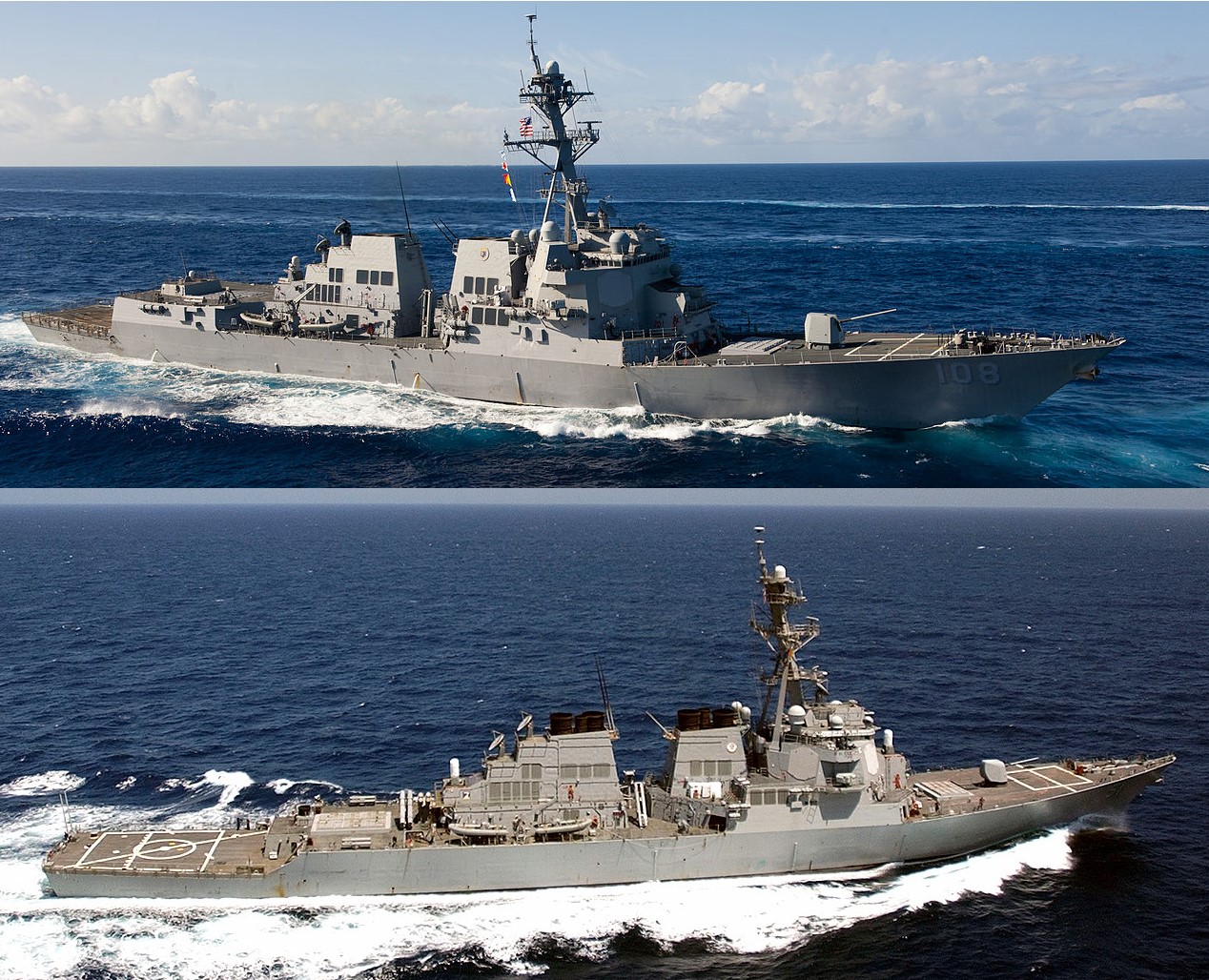
Developments in exhaust between Arleigh Burke (bottom) and Wayne E Meyer (top)
These changes are made easier by the fact that gas turbines require enormous volumes of air, dwarfing the needs of boilers or diesels, and standard practice is to simply use the ducts to bring the turbines in and out. Gas turbines also produce a similarly copious amount of hot exhaust gasses, which is a particular challenge to ship designers. The exhaust is easily capable of damaging antennas or disturbing nearby air operations, and it's a beacon to IR-homing antiship missiles. This is dealt with by drawing in extra air and mixing it with the exhaust before it is vented, greatly reducing heat signatures. One other issue is the amount of noise produced by turbines, which can require careful silencing for ships which are intended to hunt submarines. But on the whole, the benefits outweigh the drawbacks, and today, gas turbines are standard for frigates and destroyers.
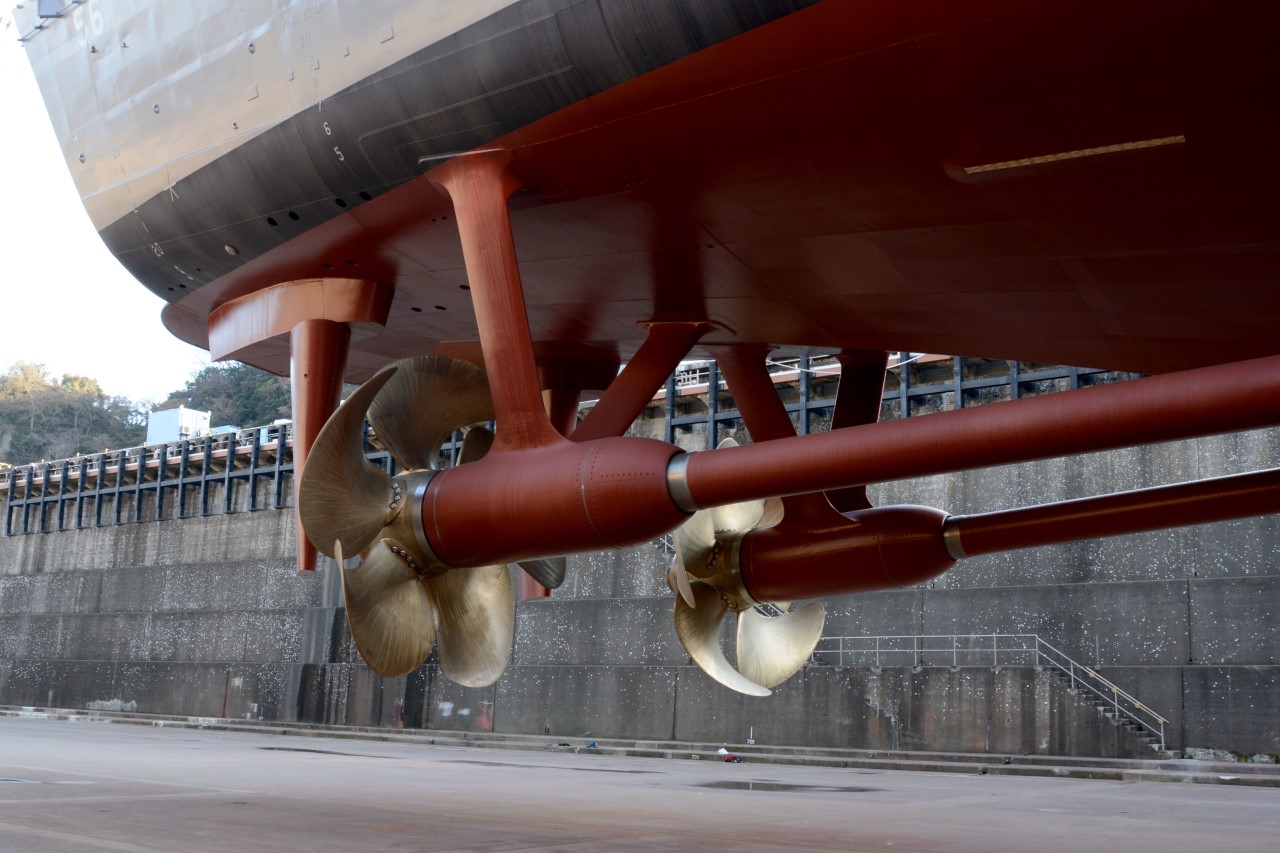
Controllable-pitch propellers on a Burke
Which isn't to say there aren't other limitations to gas turbines. While modern turbines are about as efficient as steam, this is only when they are at full throttle, and fuel economy suffers badly at lower power settings. The solution to this is the same as for diesels, with multiple turbines fitted to the same shaft. Sometimes, this just means several units of the same design, as on the Burkes and Ticonderogas, who have a pair of LM2500s on each of their two shafts. Other times, multiple types of turbines will be used, as on the British Type 42 destroyers, which had two Tynes for cruising and two Olympus turbines for high speed. One final drawback is reversing, which turbines in general are bad at. Steam turbines solved this problem with specialized reversing blades, essentially a mini-turbine that could be turned backwards, but this isn't really practical for gas. There are two solutions to this. Most western warships use controllable-pitch propellers, which allow the angle of the propeller blades to be adjusted, so it can deliver thrust either forward or backwards. The Russians have usually used a reversing gearbox instead.
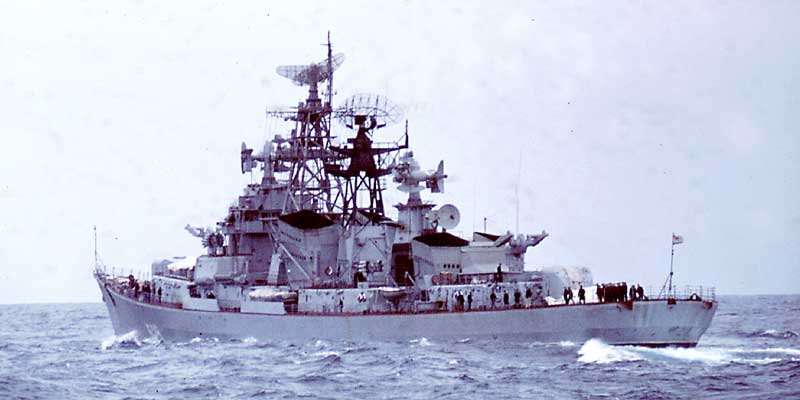
A Kashin class destroyer, showing its massive exhausts
As befitted a nation that was a pioneer in jet engine work, most of the early work done on gas turbine propulsion was British. They began this work with turbines for fast coastal craft in the years immediately after the war, and began to adopt them for larger warships in the mid-50s. In 1958, HMS Ashanti of the Tribal class frigates became the first major warship to have a gas turbine, used as a boost plant in combination with a steam turbine. It was only four years later when the first all-gas turbine plant entered service, on the Soviet Kashin class destroyers. In the US, adoption was slowed by a focus on steam (both 1200 psi oil-burning and nuclear),2 but nuclear propulsion was extremely expensive and the 1200 psi plants never worked quite right, so in 1975 the Spruance class entered service with the 4-LM2500 plant that remains standard today. Initially, these were rated at 20,000 hp each, but by the time the Burkes were designed, it had reached 25,000 hp. Continued development brought this to 29,500 hp by the early 90s, and 33,600 hp today, although the power that can be used is limited by the gearing, which was designed for the early turbines.
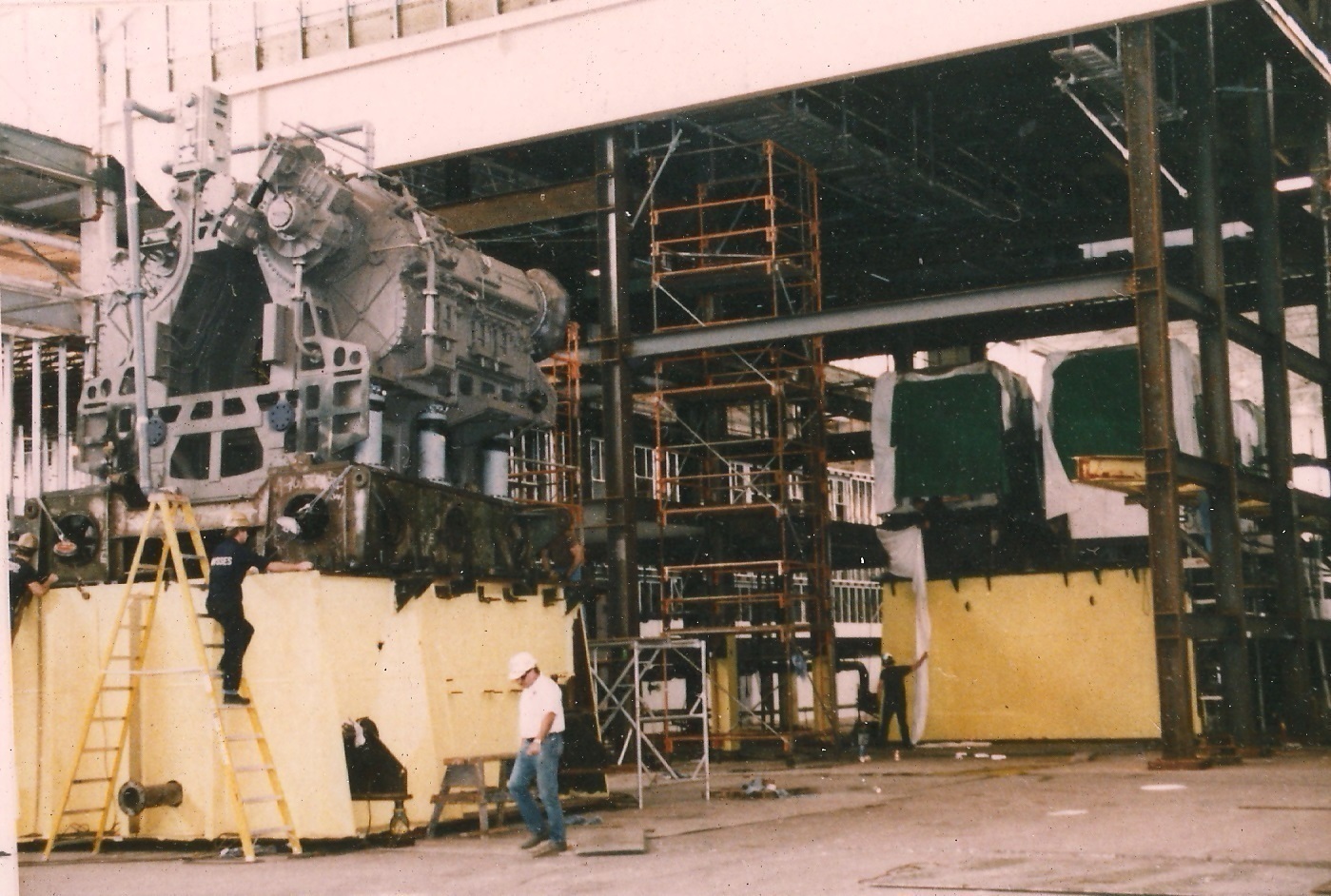
A gearbox for a Burke plant is installed in a test site
Gas turbines are powerful, compact, and reliable, characteristics which make them likely to remain a staple of naval propulsion well into the future. But even more can be done if they're combined with other systems, and the many ways this has been done will be our subject next time.
1 In fact, the first warship gas turbines used none of these. It was developed by German engineer Hellmuth Walter for propelling submarines without the use of atmospheric oxygen, and involved decomposing high-test peroxide into steam and oxygen, injecting fuel, and then igniting the result to produce the gasses for the turbine. High-test peroxide is extremely tricky stuff, and despite extensive work in Germany, the US, Britain and the Soviet Union, nothing ever came of it. Perhaps the best commentary on the process is the nickname of the experimental British peroxide submarines Explorer and Excaliber, which were known as Exploder and Exciter respectively. ⇑
2 Apparently, Admiral Rickover pushed back on gas turbine work because it would distract from nuclear plants. ⇑
Comments
You remove turbines via the ducts? That implies the ductwork has to have a) one very large intake, rather than multiple smaller ones b) be very straight (presumably)
which seems pretty disadvantageous.
On the flip side, you need big ducts because gas turbines require a lot of air, and getting complicated with them is a good way to put lots of drag in the duct and destroy your intake efficiency. As for multiple smaller ones, I'm not sure what the advantage would be.
Typo:
Pretty straight; IIRC, there are rail guides that control the path and a few turns, but none are too wild. Also, the engine itself is disassembled prior to being removed. I don't know if you can actually remove the module without cutting holes in the hull.
Those of us without any technical background appreciate "flamey end goes down" explanations.
I'm curious how combined cycle gas compares to diesel in efficiency. It sounds ridiculous, but wouldn't it be useful to have a single one for electrical generation when cruising on one turbine?
How loud are ships/subs when operating? Like, if you were swimming 100 yards away, how loud would it be? A quick google suggests a sub is about 100dB, but I'm not sure if noise for sonar purposes equates very well to noise as perceived by people. Also, if it's 100dB, that suggests that a lot of the more extreme noise control measures are sort of redundant, no? It also seems hard to square with the noise levels associated with locomotive engines and presumably similarly noisy unmuffled SSKs.
I'm pretty sure that part of that disassembly is the removal of the gas generator core, which I know comes out as a unit. I may have equivocated between that and the entire engine, which is my bad.
I'm slightly confused by what you mean here. Combined cycle gas is a specific thing that I'm covering next time, and I don't know exact efficiency numbers for it. Note that with most gas-turbine ships, the auxiliaries are just separate from the main propulsion, and power comes from either smaller gas turbines or diesels, which run independently. Exceptions discussed on Sunday.
@redRover
Decibels are even more horrible units than tons in nautical usage, so I'd guess that they're using a different baseline or something. Modern submarines are very quiet. I've heard repeatedly that modern nuclear subs produce less noise than the background (signal processing lets them be picked up) and vaguely recall hearing that the radiated noise from an Ohio class (big submarine) is under maybe 150 watts, but I can't find a source offhand. That said, submarine actions take place at thousands of yards, which does reduce the noise a bit.
Bean, did you happen to run across the rpm limits for these gas turbines? I know they can be/are different for the compressor and turbine sections, but I am curious about what they are rated to. The PW engines on the 777 are rated to about 10k for the compressor and turbine and 2,800 for the outer fan.
At first I assumed that there would be no need for a larger outer fan on what you described, but then I noticed that you mentioned cooler bypass air to mix with the hot exhaust gas so as to reduce IR signature. This led me to wonder if they do indeed have a large outer fan mounted for forcing high bypass.
We used to be taught that on very high bypass engines (777/787/400/etc) that the inner wing root mounted air-conditioning PACKS actually have a higher/"brighter" IR signature than the engines.
I know that Rolls Royce were (might still be) building 3 spool aircraft engines but I never looked into that as I assumed it was just a nomenclature context in that they were just calling the outer fan another compressor section.
My point with that though, is to ask if these maritime gas turbines have more complex compressor and turbine sections with additional gearing among those sections?
Most, though not all, maritime gas turbines are single-spool for the compressors with a separate power turbine. You could combine them, but it's a bad idea, and I know of only one two-spool compressor, although there could be more. (More on this on Sunday.)
As for actual rpm, the LM2500 (US warship standard) maxes out at 3,600, and there's no gearing between turbine and compressor. There's no outer fan. The air being drawn in is done passively, near the exhaust, and doesn't go near the turbine itself. And yes, on a three-spool engine you have one spool for the fan and two for the compressor. But a high-bypass turbofan frankly straddles the line between jet engine and gas turbine, given how much of the thrust comes from air being pushed by the fan and going nowhere near the hot bits. So by those standards, some of the most recent ship turbines are also three-spool, although the LM2500 and most other common turbines are two-spool.
Interesting on the A/C packs having a brighter signature than the engines. Could make sense, given how high the bypass is.
(Does it show that this was the one post I've written pretty much ever that was actually covered by my education?)
Wow, I didn't realize combined cycle was really a thing other than for stationary power plants. Now I'm curious who made the steam turbines on the cruise liners, because I thought nobody really made small steam equipment any more.
Thanks Bean. Another great article.
@echo
I know it's been proposed, but I'm not sure anyone has actually used it, even on a warship. Most cruise ships use diesels, possibly diesel-electric, with a few having IEP with a mix of diesel and gas.
So that's why no one ever made a gas turbine electric submersible surface vessel despite the ideal seeming such an obvious way to get higher speed out of one.
@bean
The Millenium class cruise ships have 2 LM2500+ turbines and a combined cycle steam turbine. But it obviously wasn't a good idea, since they went back to diesel-electric with azipods in the next two classes.
Interesting. Obviously, my main interest is in naval stuff, and I didn't realize that they'd actually put it on a cruise ship.
@redRover @bean
Decibels are a horrible unit everywhere: strictly they're only a relative unit of measure, but people insist on using them as absolute units with respect to unstated and arbitrary field-specific reference values.
The use of dB in popular parlance to describe loudness is based on its use in audiology, in which the 0 dB reference value is a received sound with a pressure amplitude of 20 micropascals, around the lower limit of human hearing. But decibels also get used as a measure of emitted sound power, for which there's a reference distance: if an object is emitting 0 dB of sound power, you will perceive a 0 dB sound from it when you're at a distance of 0.28 m.
So redRover's figure of 100 dB for the sound power from a submarine - a figure we might expect from noisy power tools - doesn't mean that the submarine is really loud. Conceptually, it means that if we took every sound-generating component in the submarine, squeezed them down to a point, and stuck our ear 0.28 m from it, then it would be really loud.
But there are other conventions redRover's source might have been using: there's a standard in which the 0 dB reference value corresponds to a different pressure amplitude when you're measuring it in water, and sonar operators almost certainly have their own conventions.
To really make things fun WRT decibels, decibels per square meter is also used as a measure of radar cross-section.
Can we not talk about dB? (Screams internally in Cellphone Network Hobbyist)
Having read up a bit more on gas turbines, and was surprised to see the Queen Mary 2 also uses a pair of (superstructure-mounted!) LM2500s combined with diesels to power electric azipods. Very confused about this choice, tbh.
Also surprised that a 80kt ship can make 30 knots with only 115k SHP. The smaller Montana was going to have 172k SHP to make 28 knots. Is it just a matter of hull form?
@echo, Could it be that thing about how civilian ships and military ships measure their size in tons using COMPLETELY different definitions?
No, QM2 is supposed to be about 80,000 tons displacement. It's down to hull form and length. Note that QM2 is 1132', while the Montanas were only 921'. Montana's hull speed ratio is around .689, while QM2's is .665, which indicates it should have lower SHP/ton. Though probably not that much lower. That's going to come from hull form, which is able to be optimized rather differently because you're not trying to support four turrets and a TDS. There are real costs to those, although I don't have figures to hand to indicate what they are.